Home > What is MRO?
Understanding MRO - Maintenance, Repair, and Operations
Discover how MRO processes are essential for maintaining equipment, managing assets, and streamlining operations in any industry. Gain insight into how MPulse Software can fast-track maintenance, repair, and operations.
Table of Contents
What is MRO?
MRO (Maintenance, Repair, and Operations) includes everything a company uses to keep its operations running effectively, but which doesn’t directly contribute to the production of its final product or service. It refers to materials and processes used to maintain, repair, and ensure the proper functioning of machinery, tools, and facilities across various industries. These activities are essential to minimize downtime, improve productivity, and extend the lifespan of assets, making MRO an integral part of operational efficiency.
MRO items span a wide range of categories, each playing a crucial role in maintaining the overall functionality of a business. Some common examples include:
Industrial Equipment
Components like motors, pumps, belts, and other machinery parts necessary for production or operational processes.
Consumables
Everyday items such as office supplies, cleaning products, and personal protective equipment.
Maintenance Supplies
Tools and materials like lubricants, gaskets, adhesives, and repair tools required to keep equipment and facilities in optimal condition.
Safety Equipment
Safety gear such as fire extinguishers, gas detectors, and PPE like hard hats, goggles, gloves, and safety boots ensure workplace safety.
Start your FREE TRIAL today and experience for yourself why MPulse CMMS is the preferred preventive maintenance software for over 3,000 manufacturers and facility managers
Why Is MRO Important?
MRO (Maintenance, Repair, and Operations) is crucial for the long-term success of any organization. It impacts key areas such as cost management, productivity, and procurement, all of which directly influence operational efficiency and profitability.
1. Managing Maintenance Costs
Maintaining equipment is vital to avoid frequent breakdowns and the costly consequences that follow. Neglecting regular maintenance leads to more frequent asset failures, which result in expensive repairs, production delays, defective products, idle workforce time, and missed business opportunities. Poor maintenance practices can also shorten the lifespan of machinery, forcing companies to face the choice of costly replacements or frequent, costly repairs. Whether maintenance is outsourced or handled internally, significant material and supply costs are involved, so a proactive approach to MRO is essential for controlling expenses.
2. Optimizing Inventory Control
Effective MRO management requires precise control over the procurement and management of materials, parts, and supplies. Maintenance teams often over-purchase items to avoid shortages, which can lead to excess inventory, wasted resources, and inefficient storage practices. On the other hand, poor inventory organization can lead to unnecessary reorders of items already in stock, adding to unnecessary costs. A lack of critical parts when needed—also known as stockouts—can cause extended downtime and increase repair costs. In some cases, stockouts may require expedited shipping or temporary fixes, further inflating repair costs. Proper inventory management ensures that the right parts are available when needed, without overburdening storage or the budget.
3. Enhancing Plant Productivity
Reactive maintenance—waiting for equipment to fail before addressing issues—often results in excessive and avoidable downtime, disrupting production schedules. Additionally, without comprehensive maintenance documentation, teams may waste time performing unnecessary or redundant tasks, further contributing to delays and backlogs. Stockouts, too, can halt essential repairs, leading to work stoppages and idle operators. Proactive MRO practices help minimize these issues by ensuring that equipment is regularly maintained and that parts are always available, thus keeping production lines running smoothly and reducing costly delays.
MRO plays a critical role in managing maintenance costs, optimizing inventory, and boosting plant productivity. By implementing effective MRO strategies, businesses can reduce downtime, extend equipment lifespan, and minimize operational disruptions. A well-organized MRO system allows companies to better control costs, enhance productivity, and keep operations running efficiently, ultimately contributing to long-term success and profitability.
Best Practices for an Effective MRO Strategy
By following these best practices, you can optimize your MRO strategy and achieve superior operational outcomes.
- Develop a Comprehensive MRO Plan An effective MRO strategy begins with a well-structured plan that outlines the maintenance, repair, and replacement activities necessary to keep equipment, facilities, and operations running smoothly. This plan should include a preventive maintenance schedule to ensure timely upkeep and a system for managing unexpected equipment failures. A comprehensive MRO plan will help avoid costly downtime and disruptions.
- Leverage Data and Analytics: Data and analytics are key to a proactive MRO strategy. By gathering and analyzing equipment and facility performance data, manufacturers can spot potential issues before they become critical problems. With MPulse Software, organizations can implement a predictive maintenance approach, using real-time insights to make informed, data-driven decisions about repairs, replacements, and upgrades, ultimately improving operational efficiency.
- Invest in Training and Development: Maintaining and repairing equipment requires specialized expertise. Investing in ongoing training and development for your maintenance team ensures they have the necessary skills and knowledge to handle equipment effectively and perform repairs efficiently. A well-trained team can significantly reduce the frequency and severity of breakdowns, leading to better overall performance and reduced downtime.
Utilize Technology to Streamline MRO Activities: Technology is a game-changer when it comes to streamlining MRO activities. Automation tools can simplify routine maintenance tasks, monitor equipment performance in real time, and improve repair and replacement workflows. MPulse Software is an excellent example of how technology can simplify maintenance management by keeping accurate records, identifying trends, and addressing issues early. Efficient use of technology also helps ensure consistency in documentation, making it easier to track maintenance activities and detect any emerging issues.
Implementing a comprehensive, data-driven, and tech-enabled MRO strategy is crucial for achieving optimal equipment performance, reducing costs, and enhancing overall productivity. By following these best practices and leveraging tools like MPulse Software, businesses can stay ahead of potential issues, minimize downtime, and improve long-term operational efficiency.
Benefits of MRO
Implementing MRO best practices and technologies like a CMMS can provide significant benefits that enhance nearly every aspect of your manufacturing facility:
Minimize Unplanned Downtime: A single equipment failure can halt production, leading to costly downtime. An effective MRO strategy enables proactive maintenance scheduling during off-peak times—such as between shifts or at the end of production runs. This minimizes disruptions, improves operational efficiency, increases production rates, and ultimately boosts profitability.
Enhance Worker Safety: Regular maintenance and organized workspaces help identify and eliminate safety hazards. A well-maintained facility reduces the risk of accidents and injuries, ensuring a safer work environment. This not only protects employees but also helps reduce the costs associated with workplace incidents.
Optimize Inventory Management: An automated approach to MRO inventory management ensures that your facility maintains optimal stock levels, preventing both stockouts and overstocking. With a clear understanding of when to replenish tools, parts, and supplies, you can keep inventory costs low while ensuring that necessary items are always available.
Reduce Repair Times: When spare parts and tools are organized and readily available, maintenance tasks are completed more efficiently. Advanced MRO systems can also help prioritize and plan maintenance, reducing downtime and enhancing productivity by minimizing unnecessary travel between assets or locations.
Ensure Regulatory Compliance: Strict industry regulations on safety, environmental standards, and equipment upkeep require compliance. A robust MRO strategy helps ensure that assets are well-maintained and meet these regulations. This is particularly crucial in highly regulated sectors like aerospace, government, and OEMs, where noncompliance can result in fines, penalties, and operational disruptions.
By committing to an MRO strategy focused on preventive and predictive maintenance, staff training, and data-driven technology, your organization will maintain its equipment, tools, and facilities in peak condition, maximizing productivity and reducing risk.
CMMS Software Streamlines MRO
A CMMS offers several features that streamline and enhance the MRO process for facility managers:
Centralized Data Storage: All maintenance data is securely stored in the cloud, making it easily accessible and improving decision-making.
Efficient Work Order Management: CMMS helps schedule and track work orders, reducing unplanned downtime and ensuring timely maintenance.
Asset Tracking and Management: Track assets across facilities with detailed maintenance histories, improving asset management and extending lifespans.
Inventory Management: Monitor inventory levels to avoid stockouts or overstocking, optimizing costs and ensuring parts are always available.
Performance Analysis: Evaluate asset performance to identify high-cost assets and make informed maintenance decisions.
By leveraging these features, a CMMS significantly boosts the efficiency and effectiveness of your MRO strategy.
Preventive Maintenance Blog
MPulse Means Happy Customers
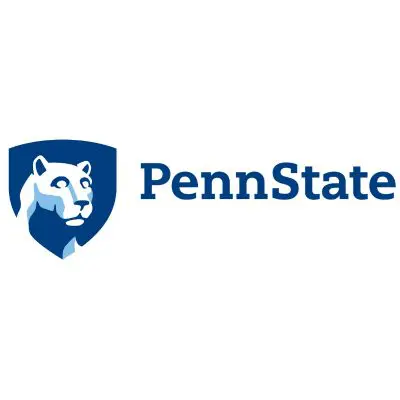
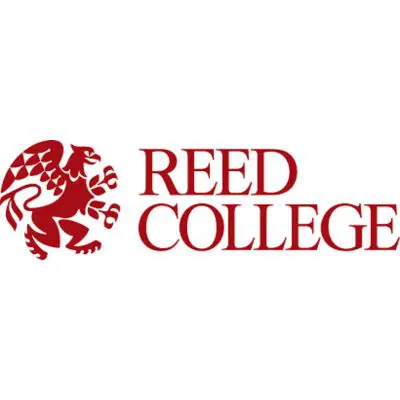
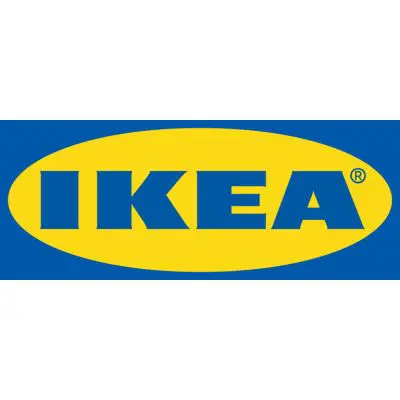
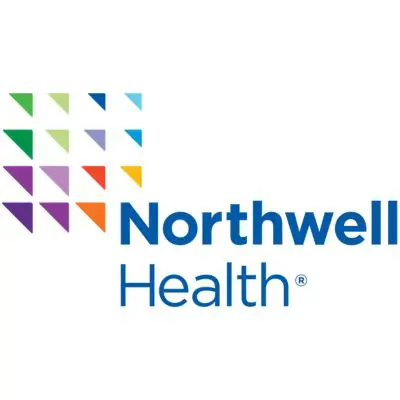
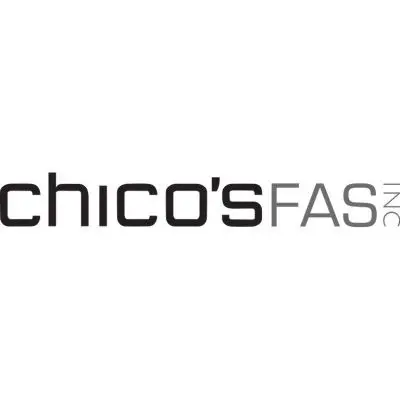
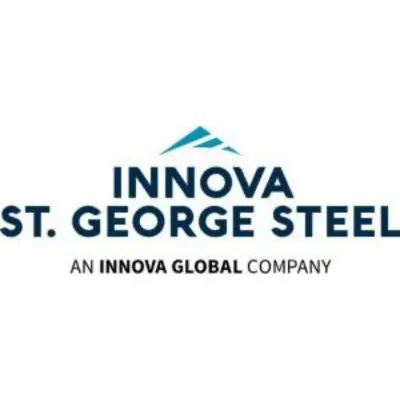