How to Prioritize Maintenance Tasks So You Can Get Stuff Done
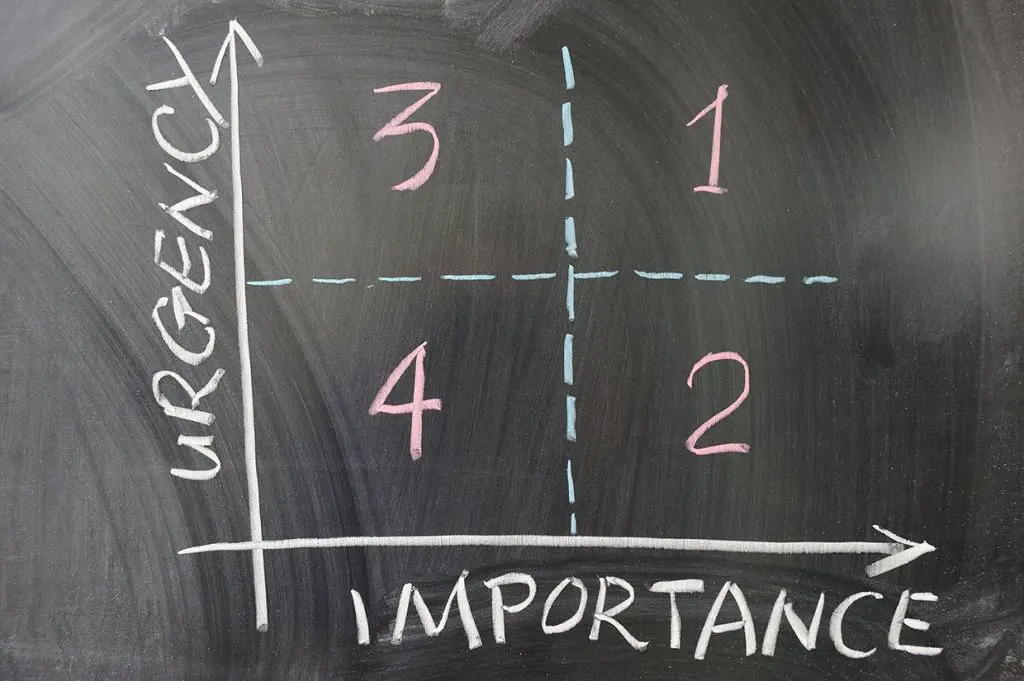
I had my whole schedule planned today—a list of tasks and plenty of time to complete them all. Guess how many I finished? Yep. Zero.
Knowing Your Stakeholder: Your Users
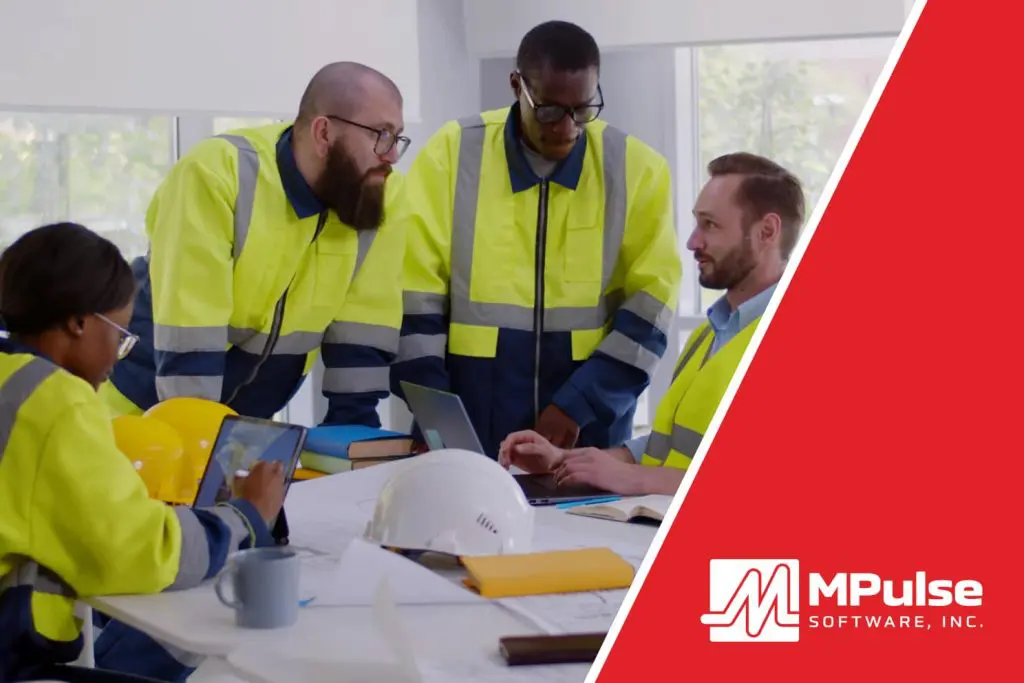
At this point, you’ve identified most of your stakeholders in the CMMS purchasing process. However, we saved the most important one for last—your users Users
Why Most Users Don’t Need a CMMS App, Part 1
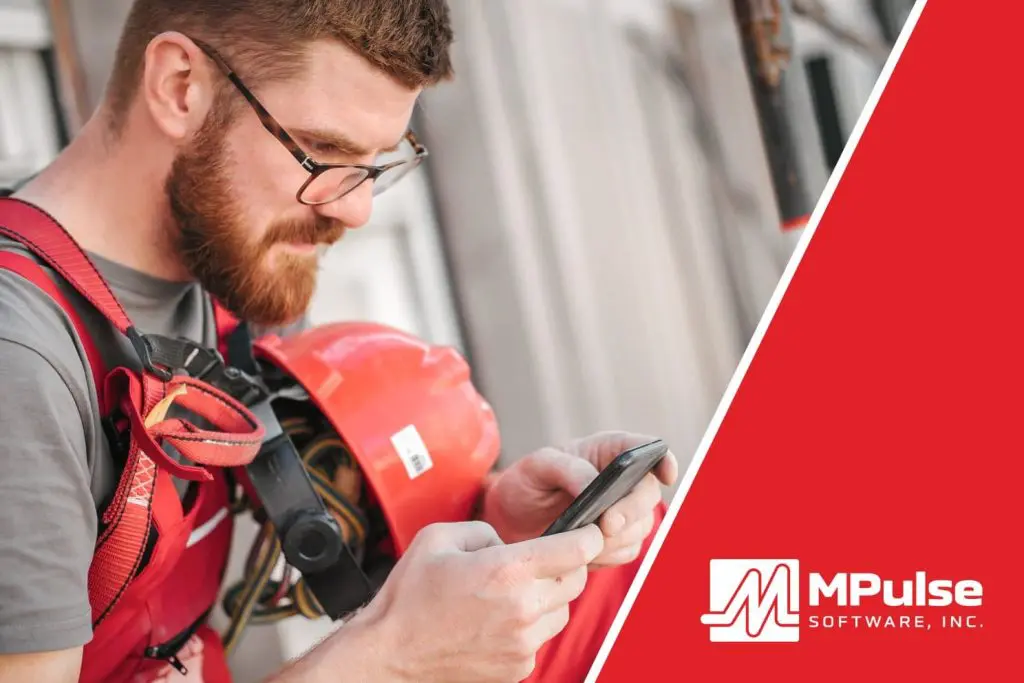
CMMS and mobile technology offer big benefits for maintainers. The ability to access information and record data on the spot—where maintenance happens, instead of in
Knowing Your Stakeholder: Legal & Compliance
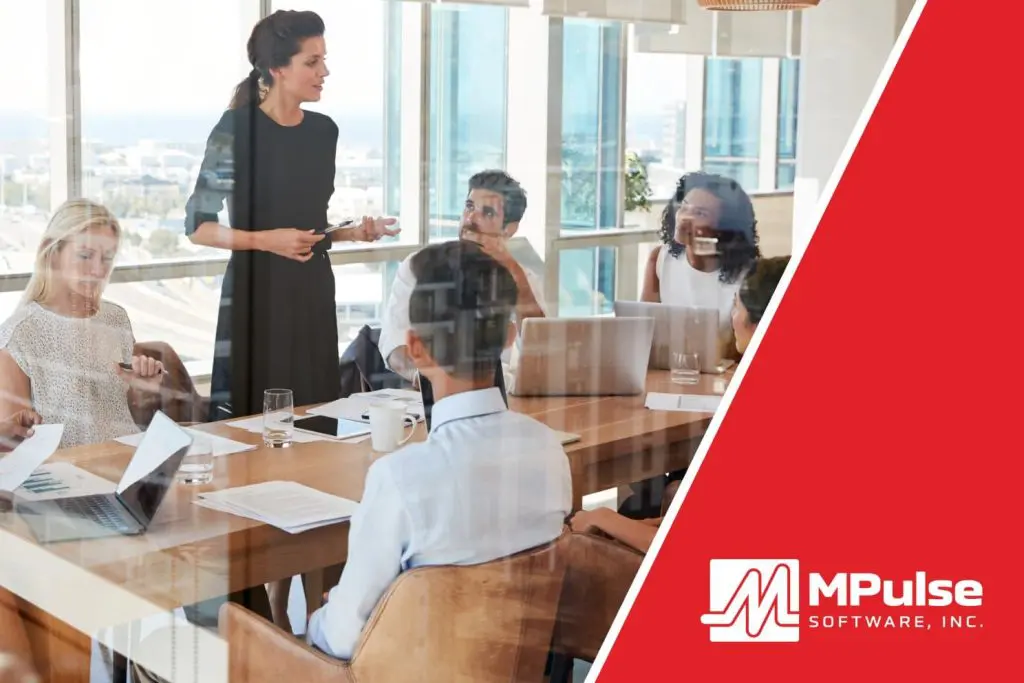
Your legal and compliance departments probably won’t use your CMMS. However, they may feel invested in what the software can do. Making a courtesy call
How to Use Reliability Centered Maintenance (RCM) to Build Efficiencies
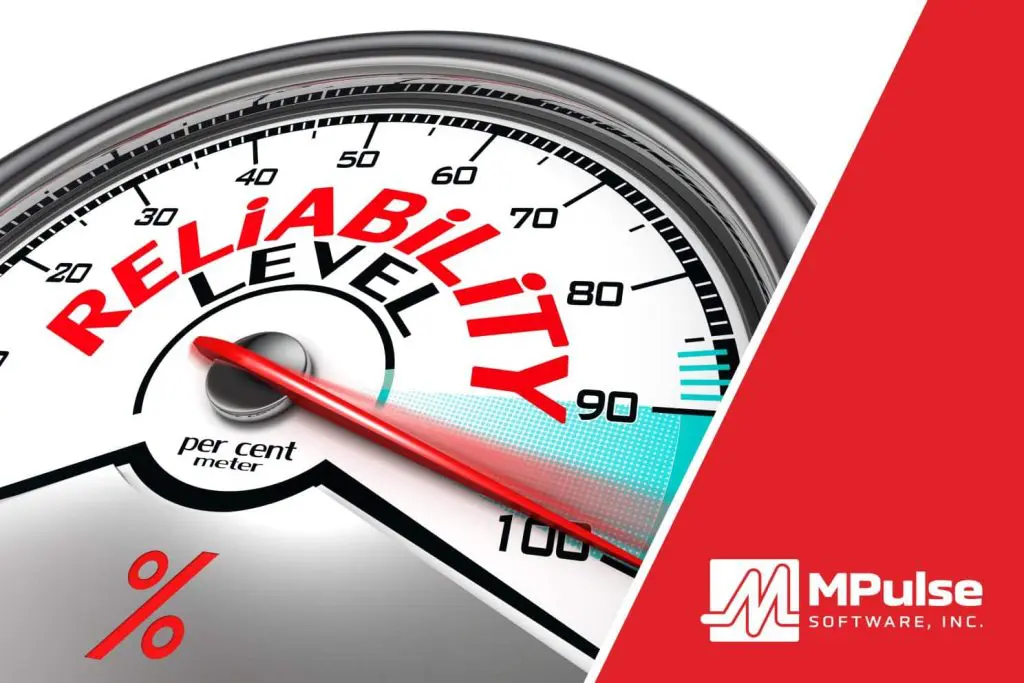
Globalization and economic pressures are forcing companies to build efficiencies wherever possible. As a result, the reliability of assets will become even more important than
How to Calculate Downtime
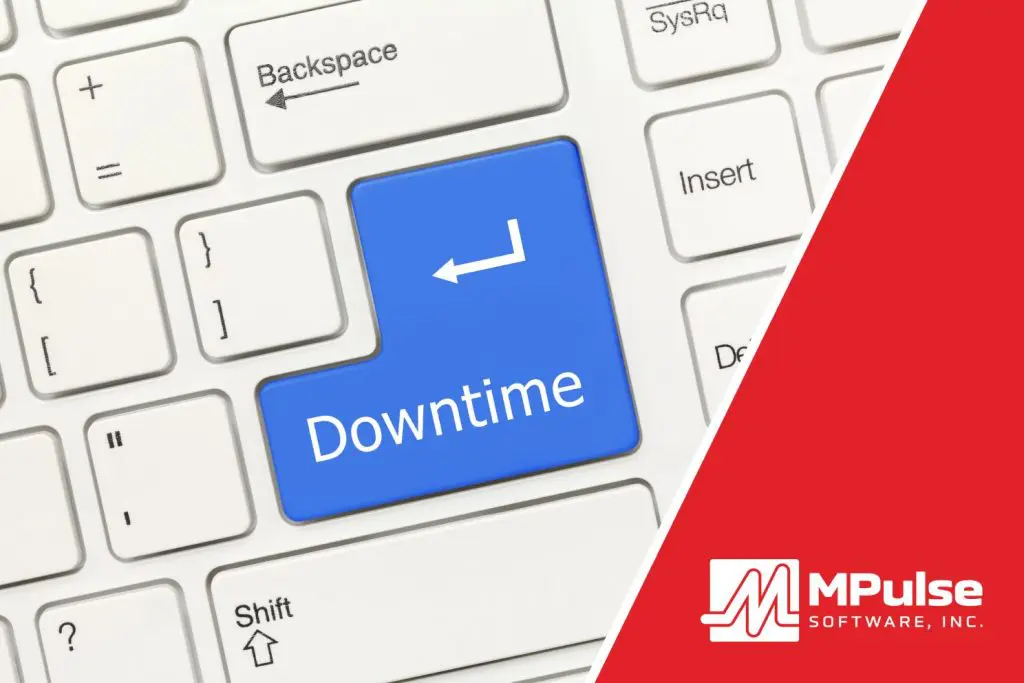
Calculating asset downtime offers new insights into your maintenance operations, and how you can make improvements. But how do you calculate downtime? And what can
How To Get The Most Out Of Your Scheduling Software
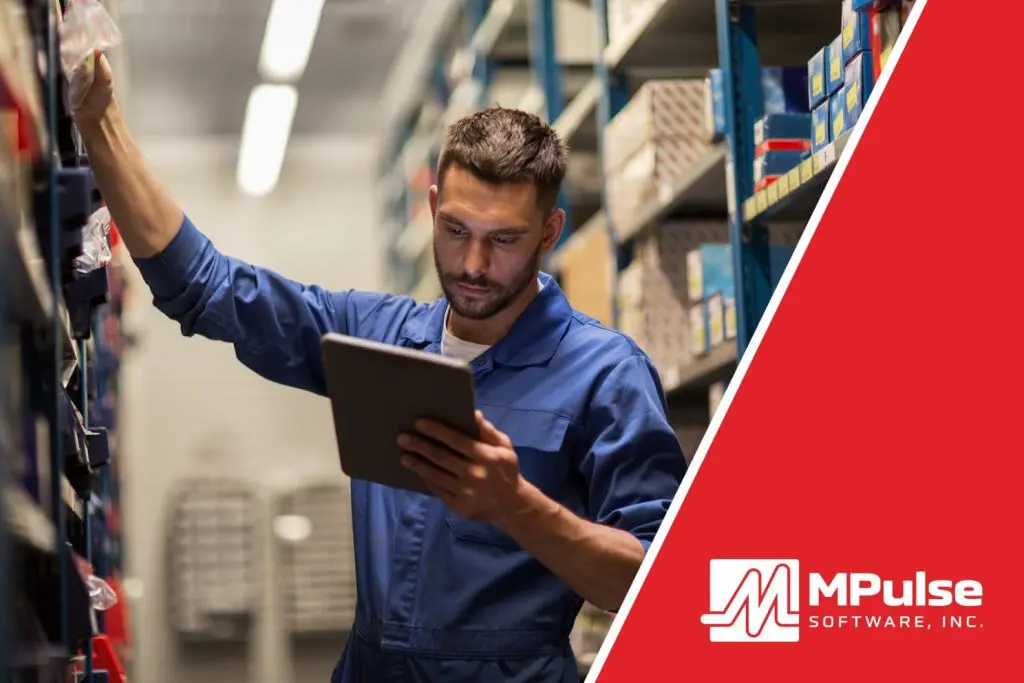
Service scheduling software always tops the list of essential maintenance management tools. Every major asset has a recommended maintenance schedule. CMMS makes it simple to
Knowing Your Stakeholder: Finance Department
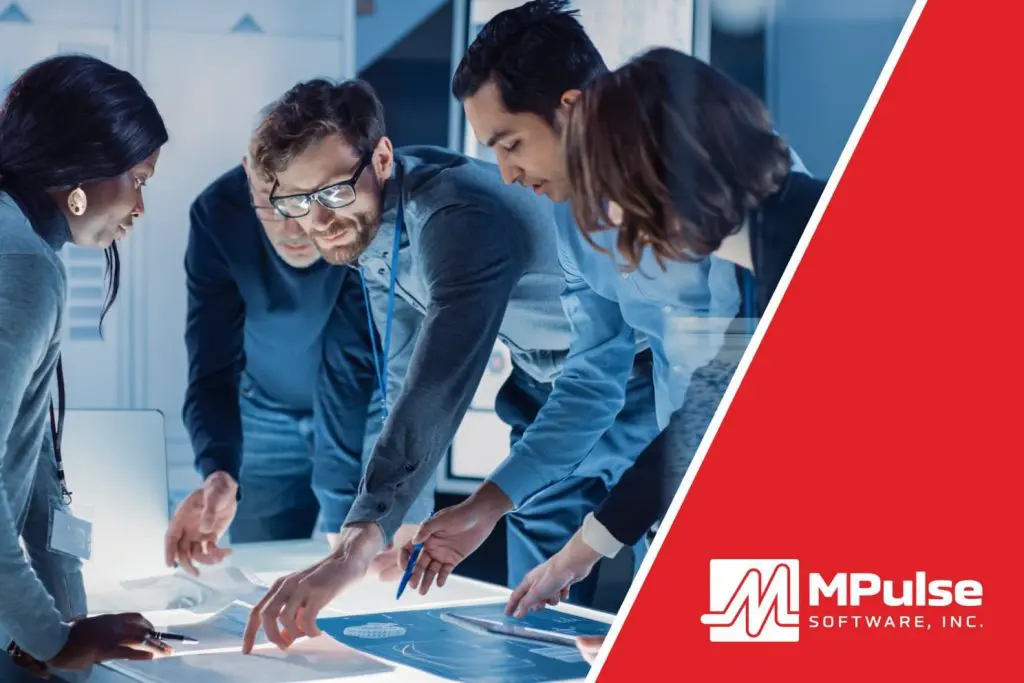
Maintenance professionals usually have the Finance department on speed dial. These two departments work together on everything from purchase orders to capital investments. Similarly, a
Six Things Your Plant Maintenance Software Needs
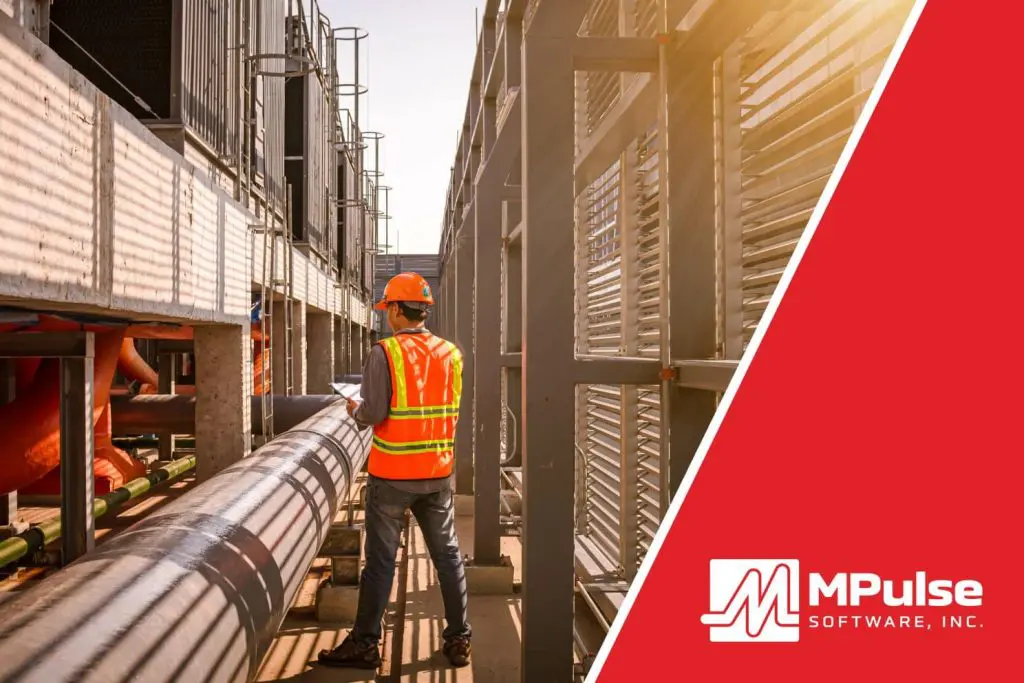
The ability to reduce maintenance expenses, minimize downtime, extend equipment life, and boost productivity sounds like a dream come true for manufacturing organizations. Plant maintenance
Knowing Your Stakeholder: Senior Managers
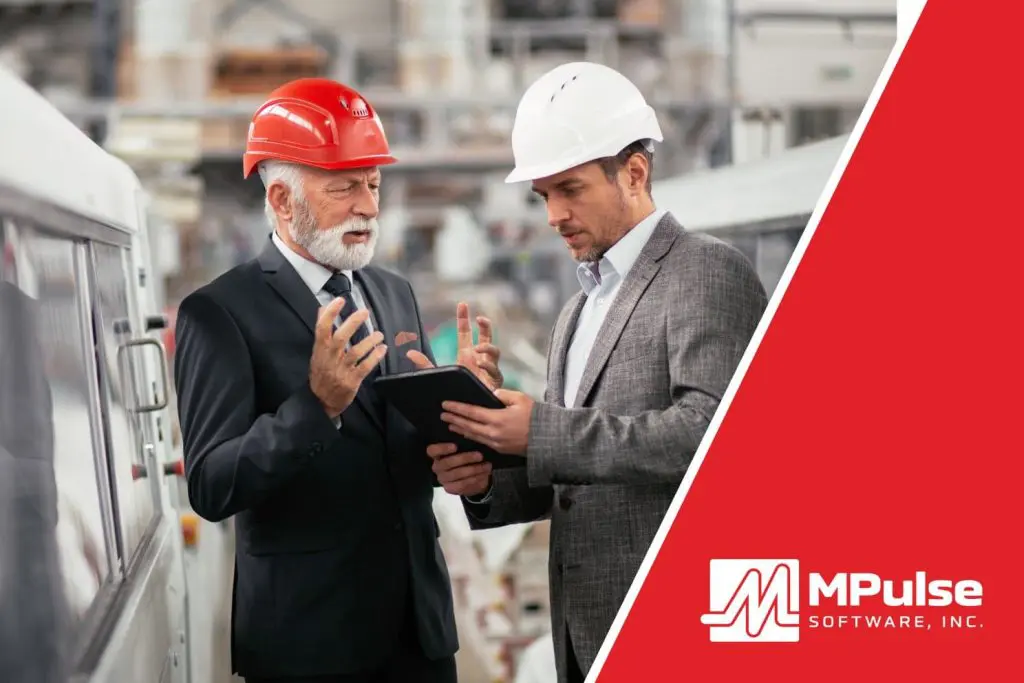
Senior managers, like your boss and their bosses, are some of the first stakeholders to consider when it’s time for new CMMS software. Their support