Using Cost Center Budgeting to Save Maintenance Dollars
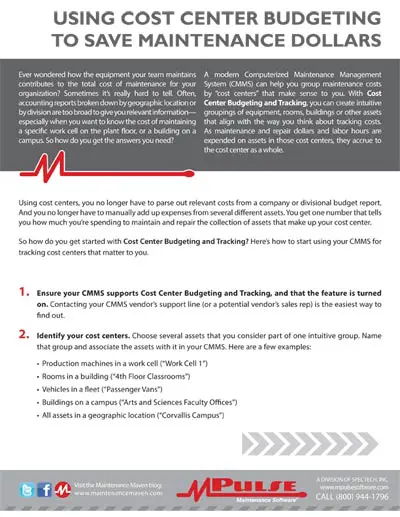
Ever wondered how the equipment your team maintains contributes to the total cost of maintenance for your organization? Sometimes it’s really hard to tell.
If your “real world” organization doesn’t align exactly with your bean counters’ accounting reports, it can be hard to see where your maintenance dollars are going.
Often, accounting reports broken down by geographic location or by division are too broad to give you relevant information—especially when you want to know the cost of maintaining a specific work cell on the plant floor, or a building on a campus.
So how do you get the answers you need? Find out how to get better visibility with cost centers.
Predictive Maintenance Data Alone is Not Enough
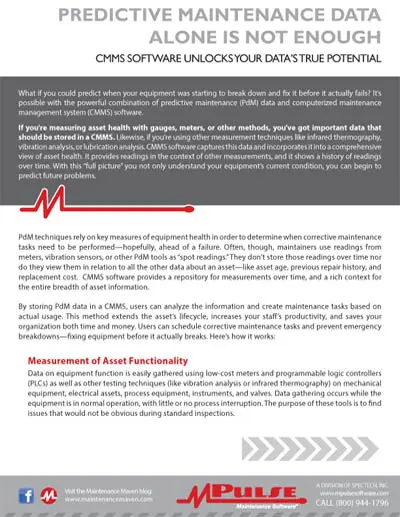
What if you could predict when your equipment was starting to break down and fix it before it actually fails?
It’s possible with the powerful combination of predictive maintenance (PdM) data and computerized maintenance management system (CMMS) software.
While PdM tools provide powerful data, that information’s value is limited without the context provided by CMMS software.
The combination of PdM data and a CMMS solution provides the most comprehensive view of your equipment.
Learn 5 important questions CMMS can help you answer to boost the effectiveness of your PM program.