MPulse Software
Barcode Scanning for CMMS
MPulse’s barcode scanning makes it easy to track assets, manage inventory, and update work orders—reducing errors and saving time.
Table of Contents
Improved Accuracy
Speed and Efficiency
Enhanced Data Accuracy
Real-Time Data Updates
The Power of Barcode Scanning
Accurate and efficient asset and inventory management is crucial for smooth maintenance operations. Manual data entry and tracking can lead to errors, delays, and inefficiencies. To streamline processes and improve accuracy, integrating barcode scanning into your CMMS is essential. Barcode scanning enables quick and reliable identification, tracking, and management of assets and inventory.
Introducing Barcode Scanning for CMMS
MPulse’s advanced Barcode Scanning feature for CMMS is designed to enhance your asset and inventory management processes. With its seamless integration, mobile device compatibility, and intuitive scanning capabilities, you can improve accuracy, speed up operations, and eliminate manual data entry errors.
Key Features and Benefits
MPulse barcode scanning solution offers the following key features and benefits:
Efficient Asset Identification and Tracking
Barcode scanning enables swift and accurate asset identification, eliminating manual data entry and reducing errors. You can effortlessly track asset movements, maintenance history, and other relevant information, ensuring up-to-date and reliable data.
Streamlined Inventory Management with Barcodes
Simplify inventory management by utilizing barcodes. Scan barcode labels on inventory items to update stock levels, track usage, and automate replenishment processes. This streamlines inventory management, reduces stockouts, and improves overall efficiency.
Barcode Integration in Maintenance Software
MPulse barcode scanning solution seamlessly integrates with your CMMS. Scan barcodes directly from the CMMS interface, linking assets, inventory, and maintenance tasks for centralized and comprehensive management.
Who uses MPulse’s Barcode Maintenance Software?
MPulse serves virtually every industry imaginable. We like to say, with a wink, “We only serve companies who work in buildings or make something.”
Our CMMS software has served more than 2,700 customers since 1995, helping them keep facilities operating at peak efficiency and manufacturing assets working at maximum productivity. MPulse is designed to grow with any size business, from small organizations with one or two maintenance technicians to global enterprises with locations around the world.
Our customers include a long list of household names like Verizon, Rolex, General Dynamics, Fender Guitars, Toyota, and Siemens. MPulse customers are located across all 50 U.S. states and in 22 additional countries around the world, on every continent … including a research station in Antarctica!
Frequently Asked Questions About MPulse's Barcode Scanning Software
Why Do I Need Barcode Scanning Software?
Barcode scanning software is one of the simplest, yet often overlooked, methods for data input and gathering. Barcodes significantly reduce human error by removing data input mistakes.
In the maintenance field, barcode data can be almost anything: stock management, inventory and parts, assets, time calculations, and much more. This data is then retrieved via a computer database, like CMMS software.
Information is one of your most important assets, and reliable data is the backbone of your operations. It helps you see your maintenance operations in a new light. You’ll also understand what’s working, and what needs more attention.
What Are the Features I'll Need?
Barcode scanning software must enable you to print barcodes that are easily read by commonly available devices—including smartphones, tablets, and barcode scanners. It should also transmit data wirelessly from barcode scanners and devices. Plus, you want your team to be able to scan a barcode to quickly record or find data in your software.
Barcode scanning software should be able to work with almost any type of data in the maintenance field, including stock management, inventory and parts, assets, time calculations, and much more. It should also streamline the purchasing and receiving process.
What if I Need to Integrate Data with Other Systems?
These days, every company relies on an assortment of systems to capture, store, and report on activities and transactions across the enterprise. Software integration enables you or your IT team to quickly and easily move data in and out of your barcode scanning software.
Many companies use data integration features to…
Import data to the software from files, databases, or other applications
Export data from the software to other applications, files, or databases
Schedule imports and exports based on times or file changes
Save “mapping profiles” to your data sources and targets
Make sure you know which applications need which type of file formats. Common ones include
Microsoft SQL Server, Oracle, Microsoft Excel, Text files, CSV files, and XML web services.
What if I Need Support?
Barcode scanning software software needs its own preventive maintenance to keep it functioning properly—just like any asset. Service updates, software maintenance, and support programs help.
Software maintenance support varies by vendor, so ask questions during your initial research. Not all software support is equal.
While we can’t claim to know how other vendors’ support programs work, our MPulse Maintenance and Support Program (MSP) partners you with our professional support team. Plus, it gives you the latest tools, free training, and software updates to keep your software optimized, and your organization on track to reach its goals.
MPulse Means Happy Customers
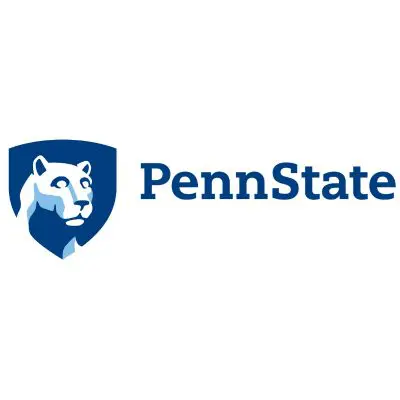
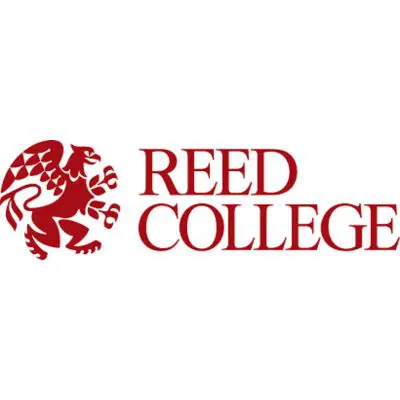
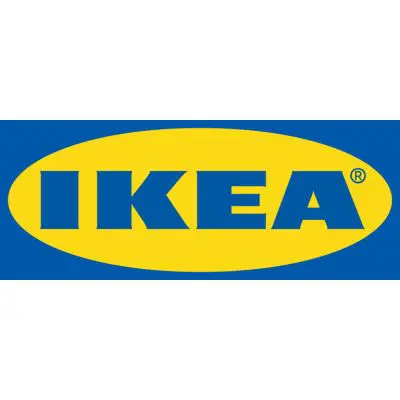
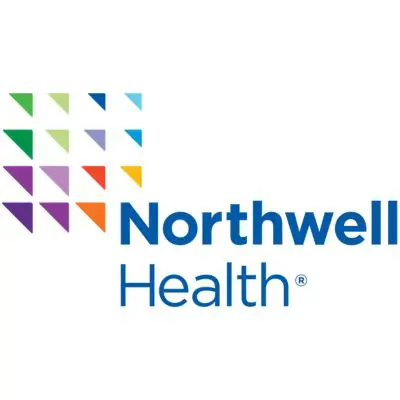
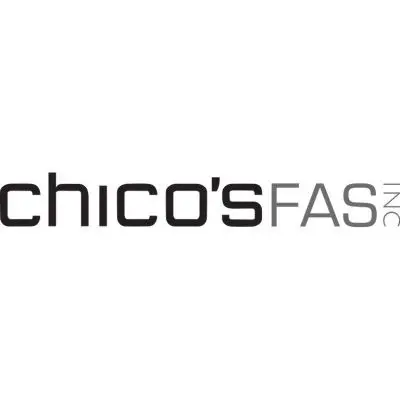
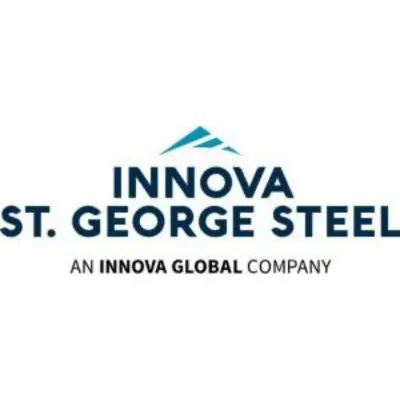
Ready to Improve Accuracy and Efficiency?
Enhance your asset and inventory management today with our industry-leading Barcode Scanning for CMMS. Improve accuracy, streamline processes, and optimize your maintenance operations. Start your free trial now!