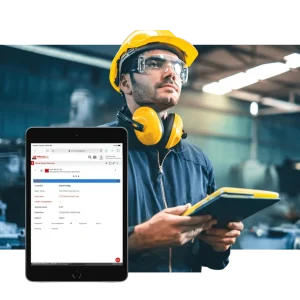
What is CMMS Software?
Explore how CMMS software can revolutionize your maintenance operations. From streamlining work order management to optimizing asset performance, MPulse Software empowers your team to proactively address maintenance needs, reducing downtime and increasing efficiency. Discover how CMMS software helps you cut costs, boost reliability, and take control of your maintenance strategy.
Table of Contents
Start your FREE TRIAL today and experience for yourself why MPulse CMMS is the preferred preventive maintenance software for over 3,000 manufacturers and facility managers
What is a CMMS?
Short for a computerized maintenance management system , CMMS is the best tool for maintenance teams to manage all of their maintenance activities in one place. This means being able to plan, track, and optimize work orders, maintenance schedules, inventory, and reporting so that critical work gets done and the results get measured.
CMMS software is a platform to mange your maintenance operations, including Reactive Maintenance, Preventive Maintenance, and Predictive Maintenance. A CMMS solution centralizes facility and equipment maintenance and can automate and enforce any maintenance task.
CMMS reports can provide insights to guide your maintenance and inspection schedules and help spot issues before they occur.
CMMS software can help with…
- Tracking work orders
- Scheduling preventive and corrective maintenance tasks
- Capturing and analyzing data
- Managing service requests
- Documenting asset information and history
- Managing inventory and parts
- Controlling the costs of maintenance
- Automating safety and regulatory compliance reporting
What features should a CMMS have?
When purchasing a CMMS, you’ll find that any high-quality computerized maintenance management system includes essential features such as work order management, scheduled maintenance planning, asset management, inventory control, maintenance reporting, and a mobile app. Leveraging these features can help resolve nearly all of your maintenance challenges. Consider the everyday obstacles your maintenance team encounters—breakdowns, backlogs, missing parts, and cost overruns, to name a few. A CMMS provides a powerful solution to tackle these issues effectively.
- Work Order Management: At the heart of any CMMS software is the work order. Whether it’s for scheduled maintenance, inspections, or unexpected repairs, maintenance managers can efficiently assign work orders to technicians or teams. Technicians with active accounts receive notifications when tasks are assigned to them. Work orders can include details such as locations, assets, parts, labor hours, costs, and other relevant data. Once completed, these orders provide valuable data to the CMMS for future reporting and analysis.
- Work Requests: A work request allows operators, technicians, janitors, staff, and others to inform maintenance management about potential issues. Through an online work request or an email, anyone can easily submit requests using their mobile device. The process is simple—just provide a brief description, specify the location or asset, maybe snap a photo of the issue, and hit submit. Once a request is created, management receives instant notifications via email and push alerts.
- Scheduled Maintenance Automation: Maximize asset lifespan, reduce downtime, and streamline maintenance processes with a powerful preventive maintenance program. Proactively address potential issues, ensure equipment reliability, and keep your operations running smoothly with ease and efficiency.
- Comprehensive Inventory Management: Robust inventory management empowers you to optimize inventory levels and prevent out of stocks. With real-time tracking and automated alerts for low stock levels, you can proactively reorder parts and supplies, ensuring they are readily available when needed. This reduces downtime and eliminates the need for emergency purchases or rush deliveries.
- Robust Reporting: A CMMS enables you to collect, analyze, and act on maintenance data by providing tools to build dashboards for real-time KPIs, create maintenance and audit logs, and generate reports on your operations. With one-click reporting, you can make informed decisions that help demonstrate the ROI of maintenance by linking better upkeep to increased production and reduced costs.
Interactive CMMS Feature Demos
What are the benefits of a CMMS?
A CMMS provides specific benefits that enhance your operations, including cost control, reduced downtime, improved efficiency, centralized information, enhanced health and safety, and robust reporting and analytics. Below are a few ways a cloud-based CMMS can support your maintenance team.
- Reduce Equipment Downtime: When implementing a CMMS, businesses can expect a significant reduction in downtime, often around 30% or more. A CMMS can significantly reduce downtime by enabling more efficient and proactive maintenance practices, leading to higher productivity and fewer disruptions to operations.
- Control Costs: Reduce unnecessary inventory expenses, minimize waste, boost uptime, and gain better control over spending. A recent IDC report shows that CMMS users achieve a 10% decrease in production-related costs.
- Increase Efficiency: CMMS users automate tasks, standardize preventive maintenance, and enhance resource accessibility to work more efficiently, safely, and boost production capacity which increases the productivity for facilities and maintenance teams.
- Centralize Information: CMMS records and tracks all maintenance activities in a centralized system. This allows you to access metrics, reports, real-time work order updates, and asset histories anytime, from anywhere.
- Improve safety: Excessive reliance on reactive maintenance is a leading cause of accidents in many production environments. A CMMS allows you to define safety requirements for each task, streamline audits, and make safety procedures easily accessible.
- Powerful Analytics: Generate real-time KPIs, create informative dashboards, and make data-driven decisions without sorting through overwhelming amounts of data.
Who uses a CMMS?
Facilities vary significantly across industries, so the individuals who require access to your CMMS will depend largely on the type of facility you’re managing. However, there are certain key roles that should generally have access to the CMMS system:
Maintenance Managers: A maintenance manager plays a key role in selecting and implementing a CMMS. Once the system is in place, maintenance managers can use it to create, schedule, and prioritize work orders, generate reports, purchase parts, and much more.
Facility Managers: Facility and operations managers use a CMMS to access maintenance data, schedules, metrics, and performance across facilities. This helps them plan production, create budgets, prepare for audits, and manage inventory purchases.
Reliability Engineers: Reliability engineers utilize the data gathered to assess asset performance and any activities that may have influenced it. They can generate reports and establish processes within the CMMS to minimize downtime, enhance efficiency, and reduce costs.
Inventory Managers: Inventory managers use a CMMS to ensure the maintenance team has the right parts, available when needed. They achieve this by tracking spare parts, setting minimum stock levels, and submitting purchase requests through the software.
Maintenance Technicians: Technicians are the primary users of the CMMS. They can access work orders, receive notifications, update asset profiles, and perform other critical tasks required for repairs and inspections.
Health and Safety Personnel: Maintenance software assists your health and safety team in gathering data for audits, accident reports, risk assessments, and more. It allows them to quickly organize and access certifications, policies, checklists, and audit results in just seconds.
Machine Operators: Machine operators use CMMS software to submit work requests and provide details for work orders, helping identify and address issues early.
Executives and Senior Managers: Business leaders utilize a CMMS to gain insights into the performance and impact of maintenance throughout the organization, enabling them to make informed decisions regarding resources and capital expenditures.
IT Department: With access to a CMMS, the IT team can oversee integrations, manage software updates, and handle data storage and security tasks carried out by the software provider.
Will CMMS help your business?
Now that you’re aware of the benefits of a CMMS, the next step is determining whether it’s the right solution for your business. While maintenance management systems were once limited to manufacturing plants, their use has now extended across various industries, including oil, gas, mining, energy, food and beverage, pharmaceuticals, chemicals, and agriculture, to name just a few.
To evaluate whether your maintenance team could benefit from a CMMS, consider these questions:
Do you manage a lot of equipment? A CMMS helps you maintain high-value assets and manage all the data from your equipment. It also assists in organizing and streamlining a large storeroom.
Do you produce a lot of goods? A CMMS is ideal for aligning maintenance with production schedules, even when they frequently change. It helps eliminate conflicts between maintenance and production teams, allowing both to focus on combating downtime, poor quality, and safety risks.
Do you aim to improve reliability? If your organization is striving for operational excellence and meeting KPI targets, a CMMS can support that goal. It enables you to move away from reactive maintenance, follow established processes, and transform inaccurate data into reliable information, ensuring smooth operations.
Why maintenance and repair teams prefer MPulse
In business for nearly 30 years, MPulse serves more than 3,000 customers around the world. Our world-class solutions provide reliable scheduling, tracking, and reporting tools for equipment and facilities maintenance organizations.
Great CMMS Software
For nearly 30 years MPulse has made high-performance software to make your job easier. Built on high-performance technology, our CMMS software is designed to grow with any size business, from small organizations with one or two maintenance technicians to global enterprises with locations around the world.
More User Licenses for Your Dollar
MPulse CMMS expands with your growing team with “concurrent user licenses,” which allow software access based on how many people are logged in at one time. For example, a team of 10 users would need 10 named user licenses, but likely 5 or fewer concurrent licenses—saving you money. Need a lot of licenses? Our Infinity Tier offers unlimited user licenses for any MPulse edition
Our Maintenance and Support Program
The Maintenance and Support Program gives you the latest tools, free training, and software updates to keep your MPulse Software optimized, and your organization on track to reach its CMMS goals. Expert MPulse employees are available from 5 a.m. to 5 p.m. Pacific Time every work day to support you. The
Buying Options That Meet Your Needs
We offer our customers FREE cloud hosting for MPulse. One buying option doesn’t fit all, so MPulse remains committed to giving customers choices by offering two ways to pay for your software: purchase MPulse outright or subscribe to our Software as a Service (SaaS) program on an annual basis.
Fast and Easy Integration
MPulse DataLink Integration Adapter allows non-techie users to map MPulse fields to other data sources and targets, creating an easy way to exchange data. You’ll have your PLCs or ERP system talking to your CMMS in no time—without expensive specialized IT support. Maintenance doesn’t happen at a desk. The MPulse CMMS Adaptive “Any Device” Interface works where you work.
Goal Oriented Implementation
MPulse has a training option to fit your budget and unique requirements. From our affordable online implementations services to our premium hands-on Assured Implementation Program (AIP), MPulse will help your team meet its goals. 97% of MPulse training grads say they expect it to improve the way they do maintenance.
A Powerful CMMS for Any Industry
MPulse Software provides solutions for all types of industries. From manufacturing to education, learn how MPulse can help you address your business’ challenges.
MPulse Means Happy Customers
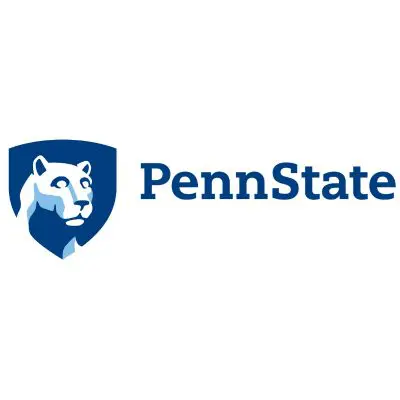
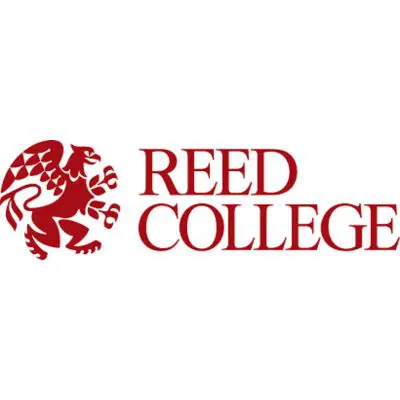
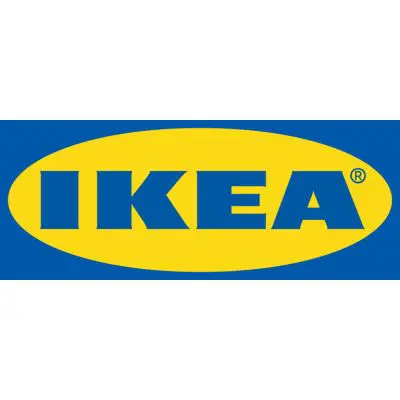
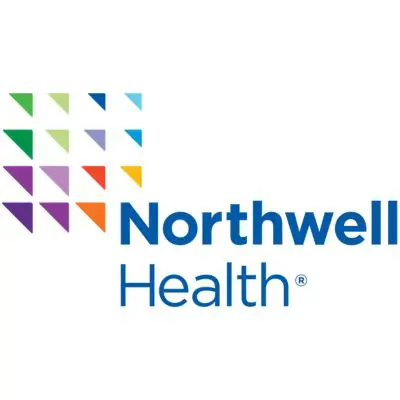
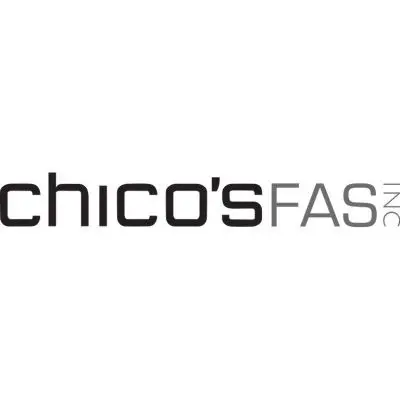
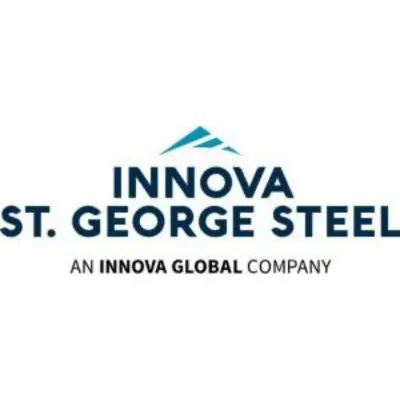