Home > About Us > Industries > What is Equipment Maintenance?
Boost Performance and Safety with Proper Equipment Maintenance
Equipment maintenance software empowers maintenance managers to proactively address issues before they escalate, preventing costly emergency repairs and minimizing the risk of unexpected breakdowns.
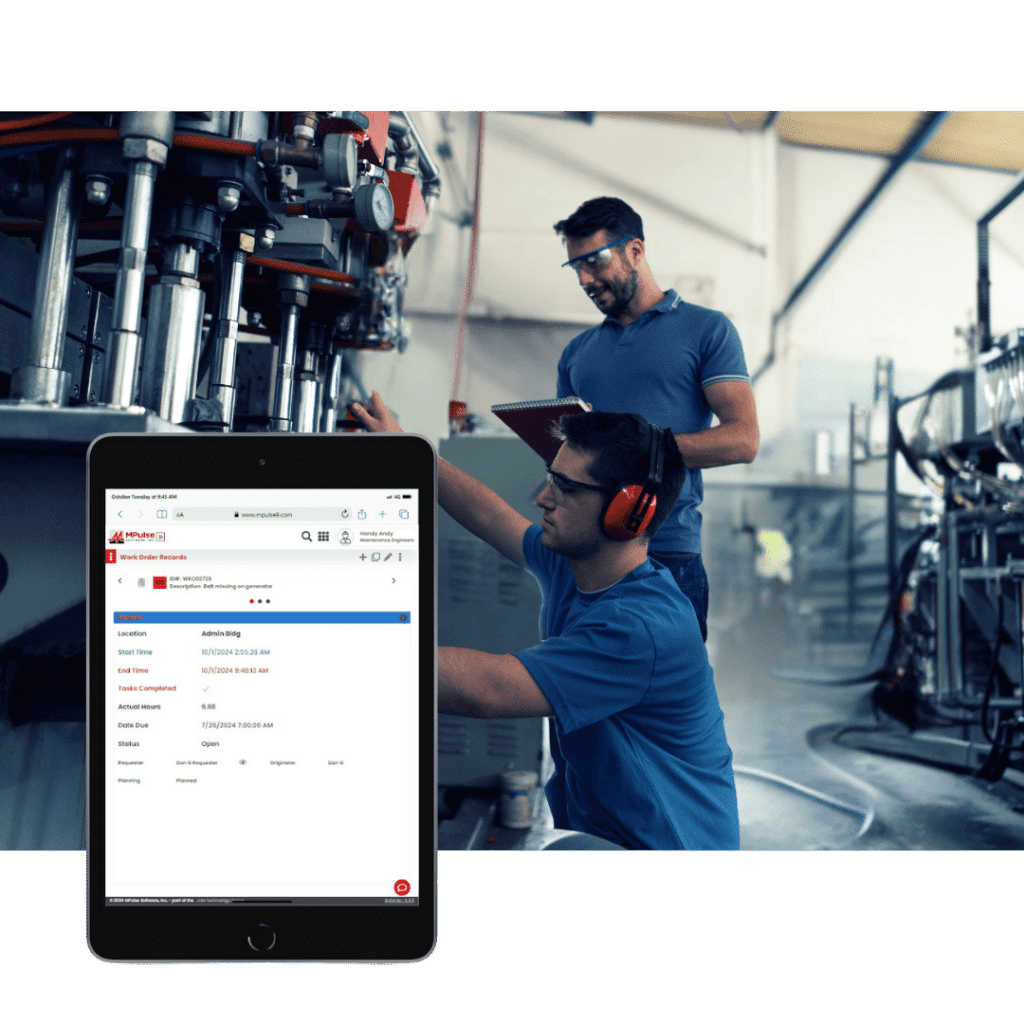
What is Equipment Maintenance?
Equipment maintenance involves systematic procedures designed to keep an organization’s assets—ranging from heavy machinery to computer systems—running smoothly and efficiently. It covers everything from routine inspections to corrective repairs, and it plays a vital role in a wide range of industries, including food service, manufacturing, hospitality, and more.
Why Equipment Maintenance is Important
Equipment maintenance is critical to the smooth operation of any organization, no matter the industry. Regular maintenance ensures that machinery, systems, and tools function efficiently and reliably, minimizing the risk of costly breakdowns and unscheduled downtime. Here’s why equipment maintenance is so important:
Minimizes Downtime
Unplanned downtime can have a significant impact on productivity and revenue. Whether it’s a production line that stops, critical machinery failing, or a vehicle breaking down, every minute of downtime can cost businesses money. By implementing a proactive maintenance strategy, businesses can reduce the likelihood of unexpected failures and ensure that operations run smoothly.Reduces Long-Term Costs
Routine maintenance helps identify and address minor issues before they evolve into expensive problems. Deferred or neglected maintenance can lead to costly repairs, part replacements, or even full equipment replacements, all of which can strain budgets. Preventive maintenance ensures that equipment is running optimally, lowering long-term operational costs by reducing major repairs and replacements.Extends Equipment Lifespan
Equipment that is properly maintained lasts longer. Regular maintenance activities like lubrication, cleaning, and inspection help reduce wear and tear, ensuring that machinery performs efficiently over an extended period. This translates into fewer replacements and better return on investment over time.Enhances Safety
Regular maintenance isn’t just about keeping equipment running; it’s also about ensuring a safe working environment. Faulty machinery can pose serious safety risks to employees, from minor injuries to fatal accidents. Routine checks and maintenance help identify potential safety hazards, reducing the risk of accidents and improving overall workplace safety.Improves Efficiency and Performance
Well-maintained equipment operates more efficiently. This can mean better fuel efficiency, improved energy use, and higher overall performance. By ensuring your assets are in peak condition, you can optimize production processes, reduce waste, and achieve greater productivity.Compliance with Industry Regulations
In many industries, equipment maintenance is not just a best practice but a legal requirement. Regular servicing and maintenance help organizations comply with local, national, and international safety regulations. Failing to meet these regulations can lead to fines, legal issues, and reputational damage.Boosts Employee Morale and Productivity
Employees are more likely to stay motivated and productive when they work with well-maintained, reliable equipment. Constant breakdowns and equipment malfunctions can lead to frustration and disruptions in work. A proactive maintenance strategy ensures that workers can focus on their tasks, without being delayed by equipment failure.
Equipment maintenance is vital for maintaining the integrity of your assets and ensuring the ongoing success of your operations. By investing in regular maintenance, you can reduce downtime, lower costs, improve safety, and boost efficiency—ultimately driving long-term business success.
Industries That Rely on Equipment Maintenance
From manufacturing plants to hospitality venues, various sectors depend on effective equipment maintenance management systems to ensure the reliability of their assets and minimize downtime. Industries using MPulse Software for streamlined equipment maintenance include:
- Food Production and Processing: Ensuring continuous uptime of production machinery.
- Aerospace and Automotive: Managing complex assembly line equipment.
- Construction and Infrastructure: Maintaining heavy machinery and building systems.
- Electric Power: Safeguarding critical systems in power generation plants.
- Manufacturing: Enhancing efficiency in consumer goods production.
- Hospitality: Ensuring operational continuity in hotels, restaurants, and more.
Best Practices for Optimized Equipment Maintenance
To maximize the lifespan and performance of your assets, consider these essential equipment maintenance best practices:
- Correct Use: Proper use is foundational to maintaining equipment. Ensure your team is trained to operate machinery according to manufacturer guidelines to avoid premature wear.
- Cleaning and Storage: Clean equipment regularly and store it in a controlled environment to prevent damage from contaminants.
- Proper Lubrication: Machines with moving parts need consistent lubrication to reduce friction and prevent excessive wear.
- Regular Inspections: Conduct frequent inspections to identify minor issues before they escalate. Key signs to look for include rust, cracks, and unusual noise or vibrations.
- Timely Repairs: Follow manufacturer guidelines for repairs and switch to a preventive maintenance approach for critical assets to reduce the likelihood of unexpected failures.
The Role of Equipment Maintenance Technicians and Managers
A successful maintenance program requires a skilled team. The roles involved in equipment maintenance include:
- Maintenance Technicians: Responsible for performing hands-on maintenance tasks, such as inspections, servicing, and repairs.
- Maintenance Mechanics: Specialize in the repair of machinery and mechanical systems.
- Maintenance Managers: Oversee the maintenance team, schedule tasks, and ensure that the necessary resources are available.
- Maintenance Engineers: Analyze and optimize maintenance operations, identifying areas for improvement.
Training and Certifications
To ensure your team is equipped to handle complex equipment maintenance, consider certifications like the Certified Equipment Manager (CEM) from the Association of Equipment Management Professionals (AEMP) or the Certified Maintenance & Reliability Professional (CMRP) from the Society for Maintenance & Reliability Professionals (SMRP).
What is Equipment Maintenance Software?
Busy construction companies need reliable equipment to deliver quality work on budget and on schedule. However, like any profession, you need the right tools.
Heavy equipment maintenance software is the best tool to create a preventive maintenance program that will help maintainers proactively conduct maintenance tasks. Therefore, you can improve heavy equipment life cycles while decreasing expensive and stressful downtime.
This technology, often called computerized maintenance management systems (CMMS), tracks work orders, schedules preventive maintenance tasks, and helps organizations control costs while documenting key data about an organization’s maintenance process. Software for heavy equipment maintenance is crucial to your business operations.
What Are the Benefits of Equipment Maintenance Software?
Staying on top of equipment maintenance—including regular planned maintenance and timely repairs on critical assets—is essential for any organization that wants to stay competitive.
When your equipment isn’t properly maintained, the risk of frequent breakdowns increases. These disruptions lead to costly downtime, putting pressure on your maintenance team to quickly restore operations and minimize production delays. Consistent, proactive equipment maintenance not only prevents these costly interruptions but also ensures that your team can focus on keeping the business running smoothly, rather than constantly reacting to equipment failures. MPulse Software can help streamline this process, allowing you to stay ahead of maintenance needs and keep your assets performing at their best.
A CMMS (Computerized Maintenance Management System) helps the maintenance team prevent unexpected breakdowns and minimize expensive downtime by:
- Eliminating Information Gaps: Ensure smooth communication between shifts by reducing confusion and errors, keeping everyone on the same page.
- Centralizing Work Order and Asset Information: Link work orders to critical asset data, enabling technicians to capture key details about repairs for better decision-making.
- Tracking Costs: Monitor personnel and vendor costs in real-time, helping you stay within budget while optimizing resource allocation.
- Easy Access to External Media: Attach and link external media files, such as photos, videos, or manuals, so technicians can access vital information quickly and efficiently.
- Work Order Status at a Glance: Instantly check the status of any work order, ensuring your team stays on track and work progresses without delays.
- Automated Scheduling: Streamline workforce management by automating schedules for both in-house employees and contract workers, improving efficiency and reducing administrative overhead.
With MPulse Software, you can leverage the power of a CMMS to ensure equipment is properly maintained, prevent costly downtime, and improve overall operational efficiency.
How MPulse Can Enhance Your Equipment Maintenance
Investing in equipment maintenance is a key strategy for improving operational efficiency and controlling costs. By using MPulse Software, you can shift from a reactive maintenance approach to a more proactive, preventive strategy. With MPulse’s Computerized Maintenance Management System (CMMS), you can track, schedule, and optimize maintenance tasks, ensuring that critical assets stay in top condition and minimizing downtime.
With MPulse, you can improve asset performance, reduce operational disruptions, and better manage maintenance budgets—turning maintenance into a strategic advantage.
MPulse Means Happy Customers
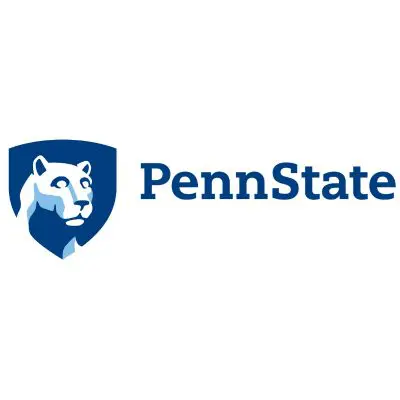
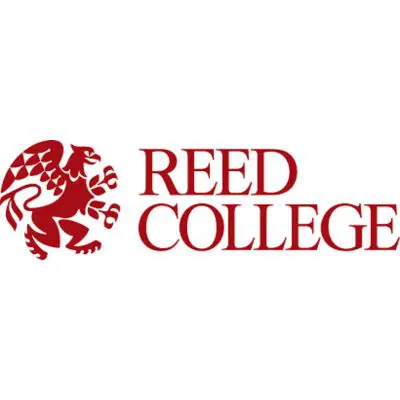
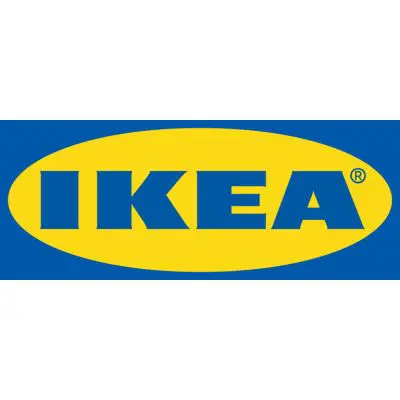
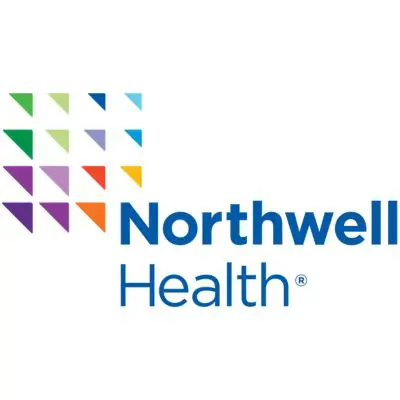
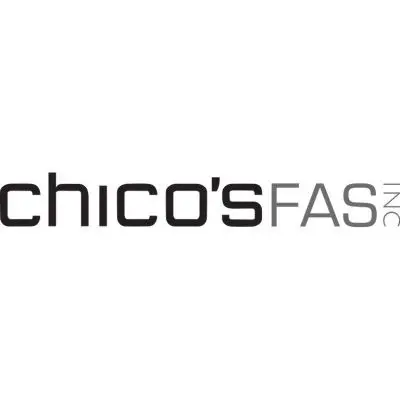
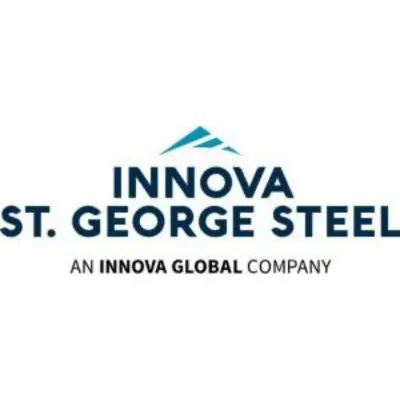