CMMS supports PFMEA by centralizing information, including data, real-time monitoring, and efficient maintenance processes. Because CMMS helps track equipment performance, spot patterns, and predict potential failures before they happen, PFMEA can identify and reduce risks more efficiently.
CMMS sends real-time alerts when equipment is not performing as expected, allowing maintenance teams to address issues early and prevent larger problems. It also keeps a record of equipment usage, repairs, and inspections, which helps refine PFMEA assessments and prioritize critical maintenance tasks.
By using CMMS with PFMEA, organizations can prevent failures, improve equipment reliability, ensure safety, and maintain smooth operations, reducing downtime and repair costs. This combination creates a strong system for managing maintenance and minimizing risks.
The Role of Maintenance in PFMEA
What Is PFMEA?
Process Failure Modes and Effects Analysis (PFMEA) looks at each step of a process to determine possible failure points (failure modes), their causes, and their effects on the process or product. Next, manufacturers can assess the risks associated with failures and prioritize actions to reduce or eliminate them. The goal is to minimize the risk of failures and improve process reliability and quality.
See how MPulse CMMS helped Siemens Building Technologies Group improve their lean manufacturing philosophy.
In short, combining CMMS with PFMEA helps manufacturers improve processes, predict and prevent equipment failures, and strengthen preventive maintenance. This approach optimizes resources, supports data-driven decisions, ensures safety, and boosts compliance, leading to a more efficient, reliable, and cost-effective operation.
Why Manufacturers Use PFMEA
Manufacturers rely on PFMEA to achieve greater reliability, product quality, and operational efficiency. Here’s a more detailed look at why PFMEA is crucial.
Risk Reduction
PFMEA helps manufacturers proactively identify potential failure points in their processes before issues arise. By recognizing these risks early, companies can take preventive measures. That reduces the likelihood of costly production disruptions, product defects, or safety incidents. This foresight is vital for maintaining a smooth and reliable production flow.
Improved Product Quality
By systematically analyzing potential failure modes and their effects on production, PFMEA enables manufacturers to take targeted preventive actions. This leads to greater product consistency and fewer defects, which not only enhances product quality but also improves customer satisfaction. With fewer errors in production, the likelihood of rework or customer complaints diminishes.
Cost Savings
The preventive nature of PFMEA translates directly into financial savings. Addressing risks before they escalate helps manufacturers avoid expensive downtime, repairs, and rework. It also reduces the possibility of costly product recalls, legal liabilities, or warranty claims. Compared to reacting after problems occur, this approach is far more cost-effective, providing long-term financial benefits.
Enhanced Safety
A key aspect of PFMEA is identifying failure modes that could lead to safety hazards for workers or end users. By addressing these risks, manufacturers can ensure safer working environments and create products that pose fewer risks to customers. This not only protects workers and consumers but also mitigates legal and reputational risks associated with safety failures.
Compliance and Standards
Many industries, such as automotive, aerospace, and medical devices, operate under strict regulations and industry standards that require robust risk management processes like PFMEA. By incorporating PFMEA, manufacturers ensure compliance with these regulations, which is essential for meeting quality, safety, and legal requirements. Compliance also helps avoid fines or penalties for non-adherence.
Continuous Improvement
PFMEA supports a culture of continuous improvement by encouraging ongoing evaluation of processes. Manufacturers can update their failure analysis as new data becomes available, leading to refined processes and ongoing enhancements in operational efficiency. This focus on continuous improvement allows companies to remain competitive in a fast-paced market.
Effective Resource Allocation
PFMEA includes the calculation of the Risk Priority Number (RPN), which helps manufacturers prioritize corrective actions based on the severity, likelihood, and detectability of potential failures. By focusing resources on the most critical risks, manufacturers can optimize their use of time, labor, and materials, improving overall productivity.
In summary, PFMEA empowers manufacturers to proactively manage risks, enhance product quality, reduce costs, improve safety, meet regulatory standards, and foster a culture of continuous improvement. This comprehensive approach leads to more efficient and reliable production systems, driving long-term success in competitive industries.
Here’s how CMMS lowers costs for manufacturers.
The Role of Maintenance in PFMEA
CMMS supports PFMEA by improving preventive maintenance and reduce operational disruptions. CMMS helps identify and address potential failures before they happen, rather than responding to them after the fact. The PFMEA process typically involves several key steps.
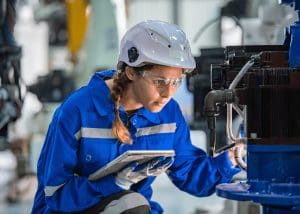
Identify Where and How a Process Might Fail
The first step is a detailed examination of each stage in the manufacturing process to uncover potential failure points. This involves looking at the machinery, tools, materials, and even human interactions that could lead to errors or breakdowns. Practitioners focus on understanding what could go wrong at each step, whether it’s a mechanical failure, a design flaw, or operational error.
Assess the Risks Associated with Process Failure
Once potential failure modes are identified, the next step is to evaluate the risks tied to each failure. This involves determining how often a failure is likely to occur (occurrence), how severe the impact would be if it does happen (severity), and how easily the failure can be detected before it causes harm (detection). This analysis helps paint a clear picture of the risk each failure mode poses to the process.
Determine the Criticality of These Risks
After assessing the risks, practitioners need to determine which failure modes are the most critical. This is typically done by calculating a Risk Priority Number (RPN) based on the severity, occurrence, and detection scores. The higher the RPN, the more urgent it is to address that specific failure mode. This step ensures that resources are focused on the most critical issues that could have the biggest impact on production or safety.
Prioritize Certain Physical Assets Based on This Determination
PFMEA doesn’t just analyze the process in a vacuum. It also looks at the physical assets involved in the process—machines, tools, and equipment—and prioritizes them based on their importance to the operation and their potential failure risks. For example, equipment that is vital to production and has a high risk of failure will receive more attention in the maintenance schedule compared to less critical or lower-risk assets.
Implement Solutions to Limit the Likelihood and Mitigate the Potential Impact of Process Failure
The final step is to implement preventive measures to either eliminate the root cause of failure or reduce its impact if it does occur. This can involve scheduling regular maintenance, upgrading equipment, adding sensors or monitoring systems to detect problems early, improving operator training, or redesigning parts of the process to be more robust. These solutions are tailored to address the most critical risks identified in the PFMEA analysis, ensuring that the likelihood of failure is reduced and that the effects of any unavoidable failures are minimized.
PFMEA improves preventive maintenance by reducing unplanned downtime, increasing safety, and making operations more efficient. The goal is to create a reliable manufacturing process where potential failures are anticipated and managed before causing disruptions.
Learn how CMMS can lower costs for manufacturers.
Key Elements of PFMEA
The key elements of PFMEA provide a structured approach to identifying, assessing, and prioritizing risks within a process. Here’s a detailed explanation of each element.
Failure Modes
This refers to the different ways a process step can fail. A failure mode could be anything that disrupts the expected outcome. Examples include equipment malfunction, incorrect material handling, or human error. Identifying potential failure modes is the first step in determining where things could go wrong.
Causes of Failure
After identifying failure modes, it’s essential to understand why these failures occur. Causes of failure are the root reasons behind a potential failure. These can be related to equipment wear, design flaws, operator error, improper maintenance, or external factors like environmental conditions. By pinpointing the exact cause, organizations can target specific actions to prevent failures.
Effects of Failure
Once failure modes and causes are identified, it’s critical to assess the impact of these failures. The effects could range from minor disruptions to major quality issues or safety risks. Understanding the consequences of failure helps prioritize which failure modes require immediate attention.
Severity
Severity measures how serious the consequences of a failure would be. The more severe the impact—such as loss of production, safety risks, or significant product defects—the higher the severity rating. This rating helps focus on the most critical failure modes that could cause the most damage if not addressed.
Occurrence
Occurrence assesses the likelihood of a particular failure mode happening. Some failures are more common due to frequent process interactions, design flaws, or poor material quality. A higher occurrence rating indicates that the failure mode happens often and needs more immediate preventive action.
Detection
Detection rates the likelihood of identifying a failure before it affects the product or process. The easier it is to detect a failure early, the lower the detection rating. A high detection rating means the failure might go unnoticed until it creates a significant problem, making early detection methods like sensors, inspections, or automated alerts crucial.
Risk Priority Number (RPN)
The RPN is a numeric score that helps prioritize which failure modes to address first. You can calculate it by multiplying the severity, occurrence, and detection ratings. The higher the RPN, the higher the risk, and the more urgent it is to implement corrective actions. This ranking system allows organizations to focus resources on the most critical issues.
Here’s why more manufacturers are switching to CMMS software.
How CMMS Supports PFMEA
CMMS supports PFMEA by improving preventive maintenance, making better use of resources, and supporting data-driven decisions, while also ensuring safety and compliance. By using these tools together, organizations can create a stronger, more efficient, and reliable operation, reducing costs and boosting overall performance.
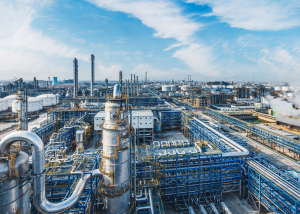
CMMS supports PFMEA efforts in the following ways.
Tracking Maintenance History
CMMS records all maintenance activities, which helps identify patterns or recurring issues in equipment that might not be apparent. This data can feed into PFMEA by providing insight into frequent failure modes and the causes behind them.
Preventive Maintenance Planning
By automating maintenance schedules, CMMS reduces the likelihood of process failures related to equipment breakdowns, which PFMEA aims to address. Properly timed maintenance can prevent failures from occurring, thus improving overall process reliability.
Real-time Monitoring and Alerts
Modern CMMS systems often include real-time monitoring of equipment performance. This data can help identify trends that may point to potential failure modes early, allowing the organization to take preventive action before a failure occurs.
Documentation of Corrective Actions
CMMS supports PFMEA by enabling the documentation of all corrective actions taken in response to failures. You can use this information in the PFMEA process to evaluate the effectiveness of previous interventions and inform future risk mitigation strategies.
Resource Management
A CMMS tracks the availability of spare parts, tools, and personnel. As a result, when failures are detected or predicted, you can identify resources to address the issue promptly. This helps in mitigating the effects of failures and ensures a smooth operation.
By using CMMS to support PFMEA, you can continuously improve processes, anticipate potential failures, and develop a robust preventive maintenance strategy.
The most important maintenance metrics and KPIs in manufacturing.
The Benefits of CMMS and PFMEA
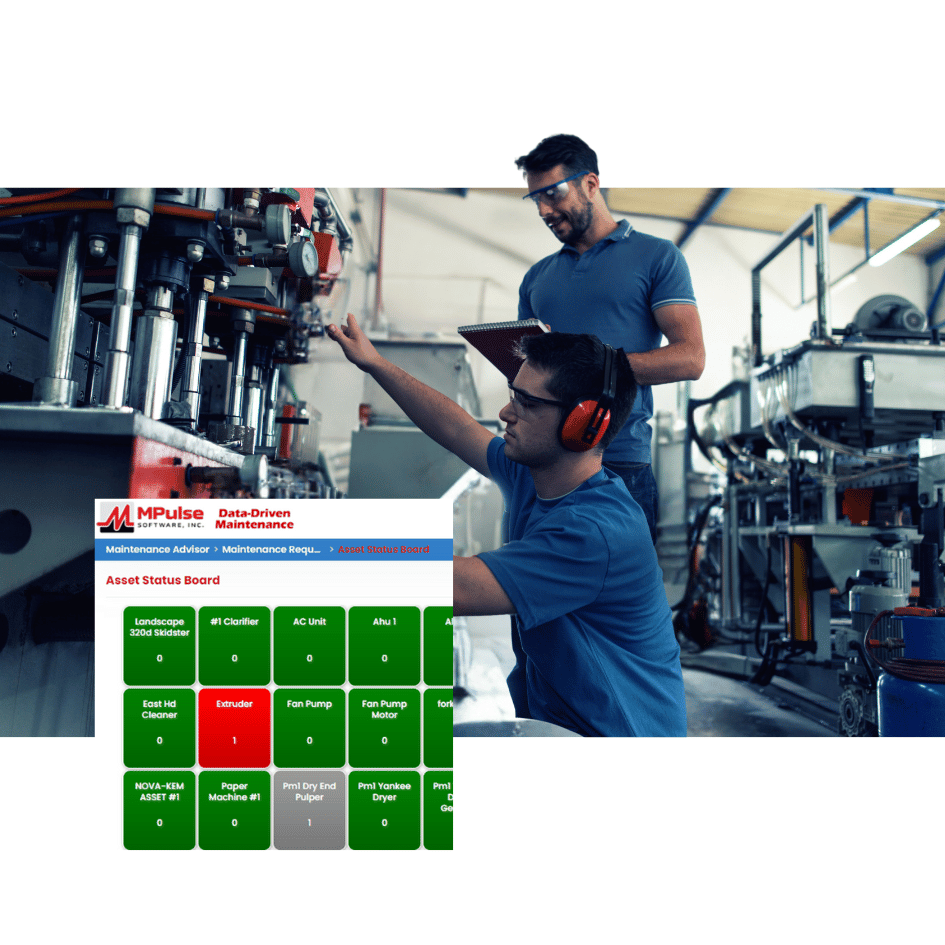
Using CMMS to support PFMEA enables manufacturers and maintenance teams to continuously enhance operational processes, anticipate potential failures, and create a strong preventive maintenance strategy. Here’s how this combination fosters continuous improvement and operational resilience.
Continuous Process Improvement
CMMS provides real-time data and historical insights into equipment performance, usage patterns, and maintenance activities. When integrated with PFMEA, this data allows teams to regularly review and update failure mode analyses based on actual equipment behavior. By continually refining PFMEA with accurate, up-to-date information, companies can identify emerging issues, improve maintenance procedures, and optimize production processes. This dynamic approach leads to constant improvements in efficiency and reliability, keeping operations competitive and agile.
Anticipation of Potential Failures
CMMS enables early detection of anomalies through real-time monitoring and automated alerts. When equipment starts showing signs of wear or irregular performance, CMMS can trigger alarms, prompting maintenance teams to act before failures occur. This proactive capability, combined with PFMEA’s structured risk analysis, allows teams to foresee and address potential failure modes well in advance. By anticipating these issues, companies can minimize unexpected downtime, prevent costly breakdowns, and reduce the likelihood of product defects or safety incidents.
Developing a Robust Preventive Maintenance Strategy
A preventive maintenance strategy aims to maintain equipment before failures occur, ensuring uninterrupted production and extending asset life. CMMS plays a critical role in developing and executing such strategies by scheduling routine inspections, tracking completed tasks, and documenting repairs. When paired with PFMEA, CMMS enhances this process by helping teams prioritize maintenance efforts based on the Risk Priority Number (RPN) and other critical factors identified through failure analysis. This ensures that high-risk assets or failure points receive timely attention, reducing the risk of critical breakdowns and improving overall operational stability.
Optimized Resource Allocation
By using CMMS in conjunction with PFMEA, maintenance teams can allocate resources more effectively. CMMS tracks the condition and performance of each asset, providing insights into where attention is most needed. PFMEA’s structured approach to identifying risks allows for more strategic decision-making when planning preventive maintenance activities. This optimized resource allocation minimizes unnecessary maintenance work, reduces downtime, and ensures that labor and materials are used where they can have the greatest impact on system reliability and safety.
Data-Driven Decision Making
CMMS stores vast amounts of operational and maintenance data, which can be harnessed to make informed, data-driven decisions. Combining this data with PFMEA insights allows organizations to base their maintenance schedules, equipment upgrades, and process improvements on actual performance data and risk assessments. This analytical approach leads to smarter, more precise decision-making, reducing the guesswork and reactive tendencies that can lead to inefficiencies or unplanned outages.
Enhanced Compliance and Safety
CMMS can be programmed to ensure that all preventive maintenance tasks meet regulatory compliance standards, providing automatic reminders and documentation of maintenance activities. When aligned with PFMEA, which helps identify potential safety risks and critical failure modes, CMMS ensures that preventive measures directly address compliance requirements and safety concerns. This dual approach helps maintain a safe working environment and keeps the company in line with industry standards and regulations, reducing the risk of fines, accidents, or legal liabilities.
In short, combining CMMS with PFMEA helps manufacturers improve processes, predict and prevent equipment failures, and strengthen preventive maintenance. This approach optimizes resources, supports data-driven decisions, ensures safety, and boosts compliance, leading to a more efficient, reliable, and cost-effective operation.