Streamline Inventory Tracking and Replenishment with
Spare Parts Inventory Management System
Spare Parts Inventory Management System
Use the MPulse Spare Parts Inventory Management Software to get real-time visibility of parts and supplies inventory, and manage stocking and reorder levels.
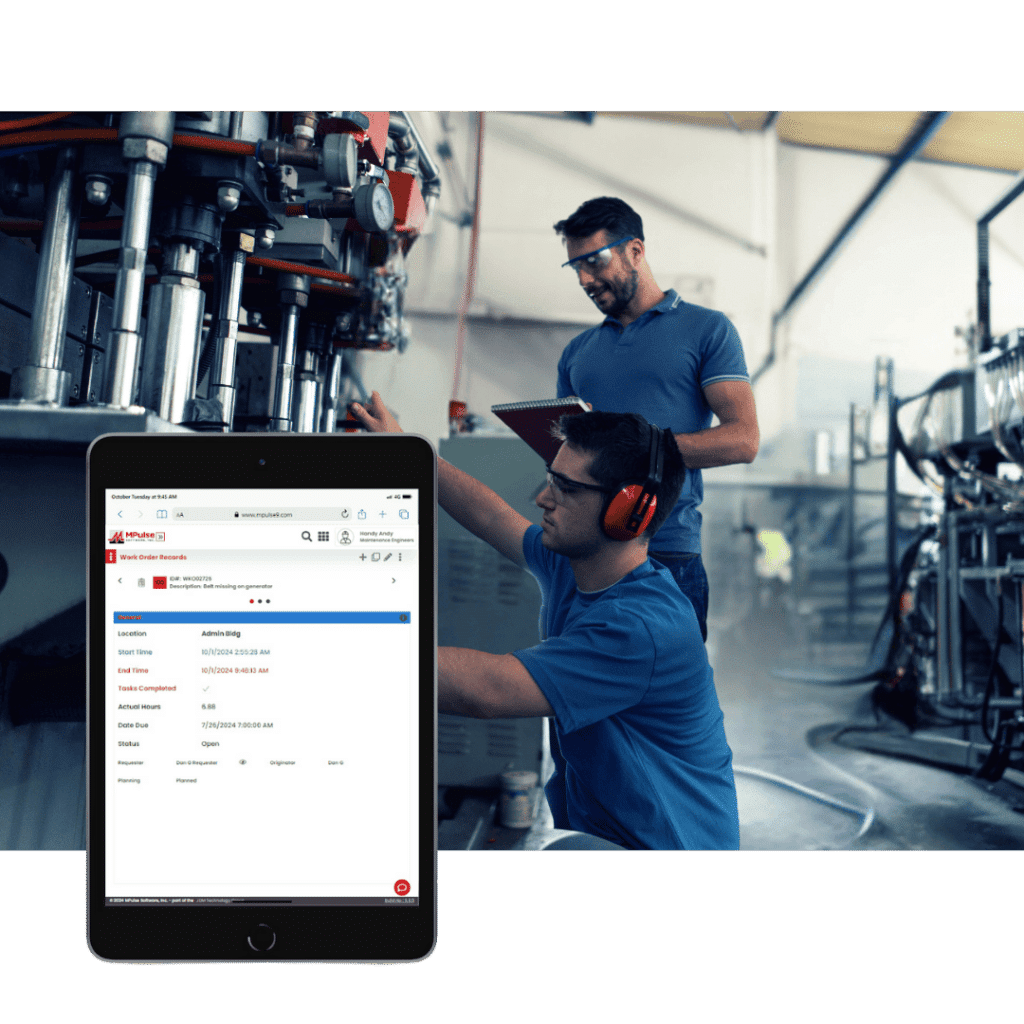
Introducing the MPulse Spare Parts Inventory Management System
MPulse’s advanced Parts and Supplies Inventory Management functionality is specifically designed to address these challenges and streamline your inventory management processes. With its powerful features and intuitive interface, you can efficiently track inventory, optimize stock levels, and ensure timely availability of parts and supplies.
Streamlined Inventory Tracking
Efficient Replenishment
Optimize Stock Management
Time and Cost Savings
The Challenges of Spare Inventory Management Systems
Effective spare parts inventory management is vital for ensuring smooth maintenance operations and minimizing costly disruptions. However, manual inventory tracking and replenishment processes can be time-consuming, error-prone, and result in inefficient stock management. Dealing with stockouts or excess inventory can lead to increased downtime, wasted resources, and reduced productivity. Use the MPulse Spare Parts Inventory Management System to get organized, save time and money, and reduce downtime.
Why Choose MPulse Spare Parts Inventory Management System
Optimize Inventory Levels and Reduce Stockouts
MPulse inventory management software empowers you to optimize inventory levels and prevent stockouts. With real-time tracking and automated alerts for low stock levels, you can proactively reorder parts and supplies, ensuring they are readily available when needed. This reduces downtime and eliminates the need for emergency purchases or rush deliveries.
Efficient Stock Management and Ordering
Say goodbye to manual inventory management! MPulse software streamlines stock management and ordering processes. You can track inventory levels, set reorder points, and automate reordering based on predefined rules. This eliminates guesswork and reduces the risk of stockouts or overstocking, saving time and resources.
Track Usage History and Availability
Gain insights into the usage history and availability of parts and supplies with the MPulse Spare Parts Inventory software. Track the consumption patterns of specific items, analyze historical data, and make informed decisions regarding inventory levels and reorder quantities. This data-driven approach helps you optimize stock management and streamline your procurement process.
Who uses MPulse Spare Parts Inventory Management System?
MPulse is designed to grow with any size business, from small organizations with one or two maintenance technicians to global enterprises with locations around the world. We serve virtually every industry imaginable. We like to say, with a wink, “We only serve companies who work in buildings or make something.” Those companies have the opportunity to benefit from the Spare Parts Inventory System that’s included with this CMMS package.
MPulse Maintenance Software has served more than 2,700 customers since 1995, helping them keep facilities operating at peak efficiency and manufacturing assets working at maximum productivity. Our customers include a long list of household names like Verizon, Rolex, General Dynamics, Fender Guitars, Toyota, and Siemens. Our customers are located across all 50 U.S. states and in 22 additional countries around the world … including a research station in Antarctica! The built-in Spare Parts Inventory Management System helps them ensure that when their Assets need work, they have the spare parts inventory available to do the job!
Frequently Asked Questions About MPulse Parts & Supplies Inventory Management
What if I need to manage parts and supplies in more than one location?
MPulse Multisite Connector provides a universal framework, which connects all the locations across your distributed enterprise. That means you can have truly global settings, global reporting, and—yes, that’s right—enterprise-wide inventory search and transfer. So, you’ll know what inventory is available across the company, not just in your local storeroom.
Enterprise Inventory Transfer Manager is a feature of MPulse Multisite Connector. It allows you to do things like…
- Discover available inventory in other storerooms across the enterprise
- Issue an interoffice request to retrieve parts
- Track the fulfillment and transfer process
Plus, you ‘ll have all the standard capabilities of our Parts & Supplies Inventory Management feature—such as stocking levels, reorder points, storage locations, and supplier information. You can also track various units of measure for a single inventory item. For example, you might purchase oil by the barrel, but use it by the quart.
Learn more about how to take multisite inventory to the next level.
Can Inventory Parts and Supplies Management help with inventory audits?
CMMS software is the best way for maintenance and facility management teams to prepare for inventory audits.
CMMS software helps in several ways…
- Preparation Time: Scheduled audits require gathering paperwork beforehand, which can be tedious and time-consuming when it involves sifting through stacks of paperwork. With CMMS software, accurate reports are easy to pull together in just minutes—saving a lot of time and frustration.
- Verifiable Data: CMMS software records all your parts tracking, stocking, ordering, and inventory processes with every work order. When it’s time for an audit, the data is easier and faster for auditors to verify.
- Easy Access: Instead of pulling out binders of paperwork, auditors can sit down at a computer to find the information they need. With CMMS software, the answers are at their fingertips.
Discover how MPulse can help when it’s time for a parts room audit.
Can Inventory Parts and Supplies Management help with cyclical inventory counts?
Many organizations conduct an annual inventory for tax and financial accounting purposes. But others prefer cyclical inventory counts, where the team inventories 1/12 of the stockroom on a monthly basis, or ¼ on a seasonal basis. That can significantly cut down the time spent on counting inventory.
Cyclical inventory counts are easier to conduct with normal operations, which minimizes disruptions. The increased frequency also makes it easier to identify inventory management issues and correct them. It can also increase stock turns and reduce inventory costs by minimizing the time that stock spends in your inventory.
Here are four ways to control inventory costs with CMMS software.
Preventive Maintenance Blog
Ready to Streamline Your Spare Parts Inventory Management System?
Take control of your inventory management today with our industry-leading Parts and Supplies Inventory Management Software. Optimize stock levels, prevent stockouts, and improve efficiency. Start your free trial now!