Five Ways CMMS Can Save You Money
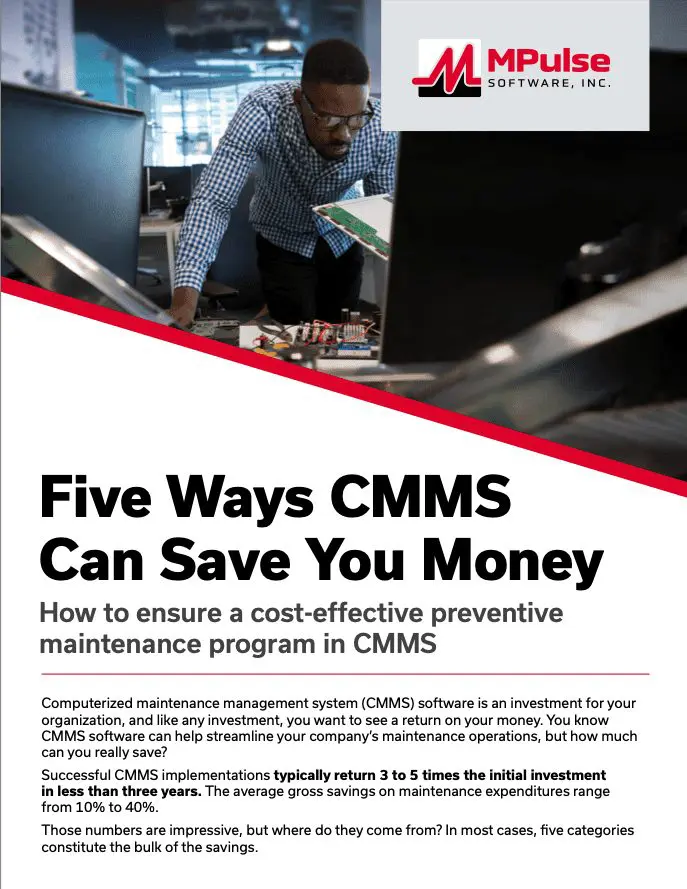
Show me the money!
Computerized maintenance management software (CMMS) is an investment for your organization, and like any investment, you want to see a return on your money.
You know computerized maintenance management software can help streamline your company’s maintenance operations, but how much can you really save?
Successful CMMS implementations typically return 3 to 5 times the initial investment in less than three years. The average gross savings on maintenance expenditures range from 10% to 40%.
Those numbers are impressive, but where do they come from? In most cases, five categories constitute the bulk of the savings.
Use Your CMMS Power Wisely
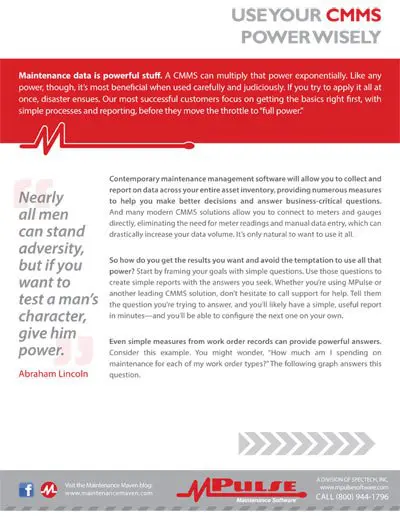
Maintenance data is powerful stuff. A CMMS can multiply that power exponentially.
Like any power, though, it’s most beneficial when used carefully and judiciously. If you try to apply it all at once, disaster ensues.
So how can you keep your reporting simple and focused on the questions that matter most to you?
Our most successful customers focus on getting the basics right first, with simple processes and reporting, before they move the throttle to “full power.”
Learn how.
CMMS By The Numbers
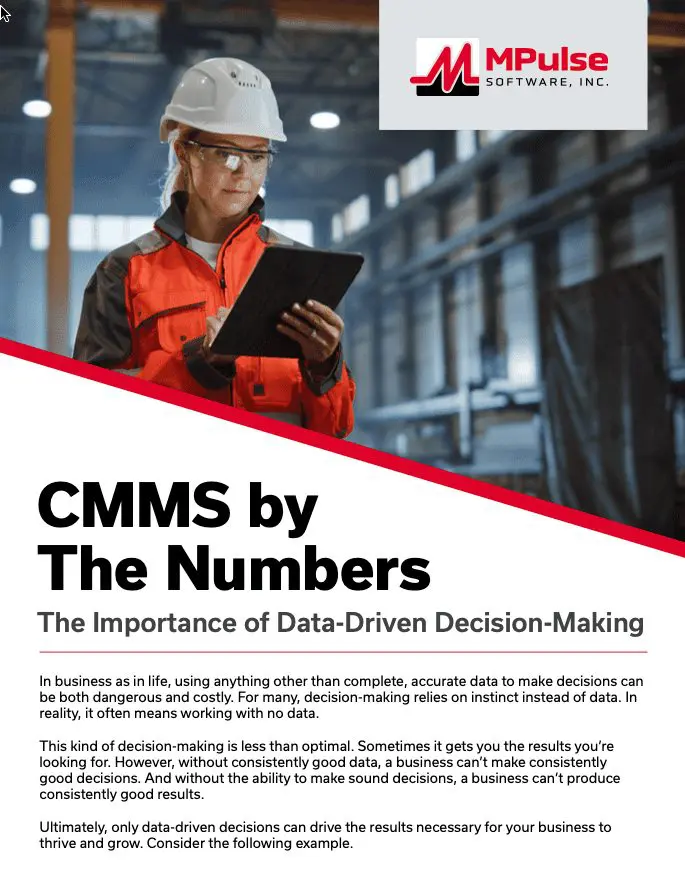
Don’t rely on intuiting the right answers for your critical business decisions. Your CMMS is a treasure trove of valuable information.
Without consistently good data, a business can’t make consistently good decisions. And without the ability to make sound decisions, a business can’t produce consistently good results.
Ultimately, only data-driven decisions can drive the results necessary for your business to thrive and grow.
Ask yourself whether it’s possible to support your decisions with numbers. You’ll quickly see the results in the most important place of all—your bottom line.
What are Your Pain Points?
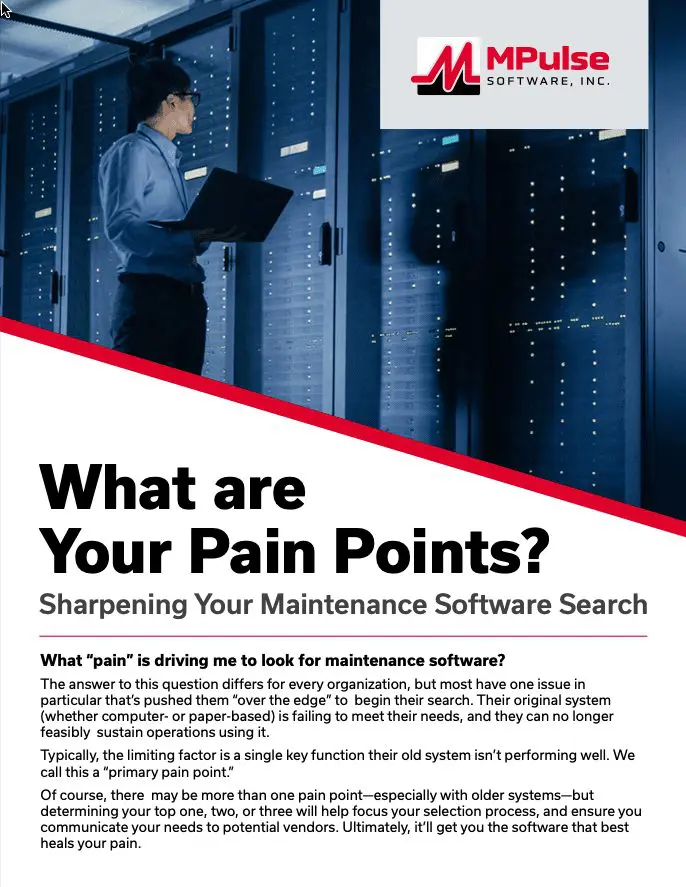
What’s driving you to search for CMMS software?
The answer to this question differs for every organization, but most have one issue in particular that’s pushed them “over the edge” to begin their search. Their original system (whether computer- or paper-based) is failing to meet their needs, and they can no longer feasibly sustain operations using it.
Typically, the limiting factor is a single key function their old system isn’t performing well. I call this a “primary pain point.” Of course, there may be more than one pain point—especially with older systems—but determining your top one, two, or three will help focus your selection process, and ensure you communicate your needs to potential vendors. Ultimately, it’ll get you the software that best heals your pain.
What to Look for in Maintenance Management Software
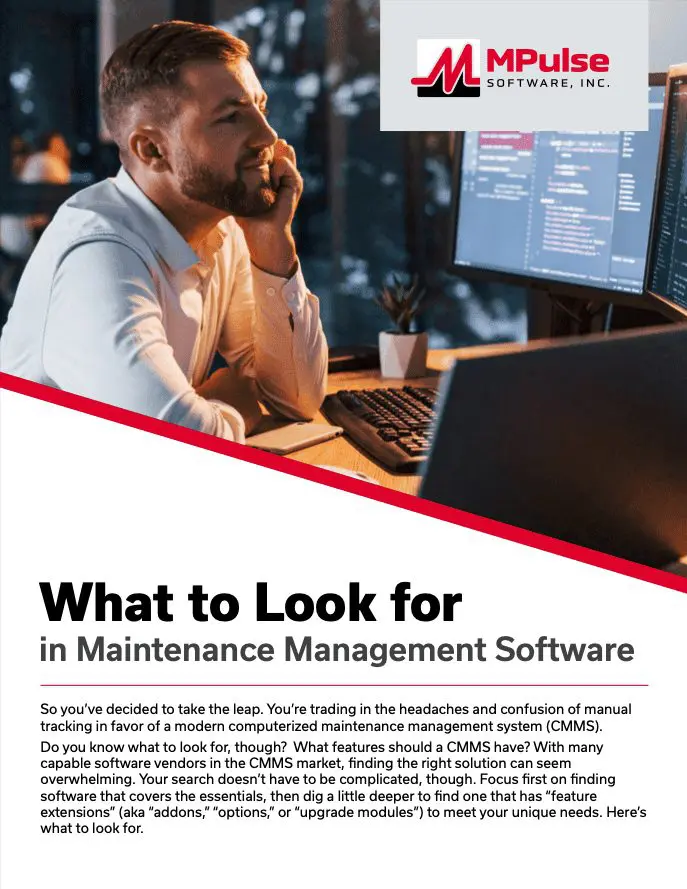
Understand the basic and advanced features of contemporary maintenance management software to guide your software search.
So you’ve decided to take the leap. You’re trading in the headaches and confusion of manual tracking in favor of a modern computerized maintenance management system (CMMS).
Do you know what to look for, though? What features should a CMMS have? With many capable software vendors in the CMMS market, finding the right solution can seem overwhelming.
Your search doesn’t have to be complicated, though. Focus first on finding software that covers the essentials, then dig a little deeper to find one that has “feature extensions” (aka “addons,” “options,” or “upgrade modules”) to meet your unique needs. Here’s what to look for.
Predictive Maintenance Data Alone is Not Enough
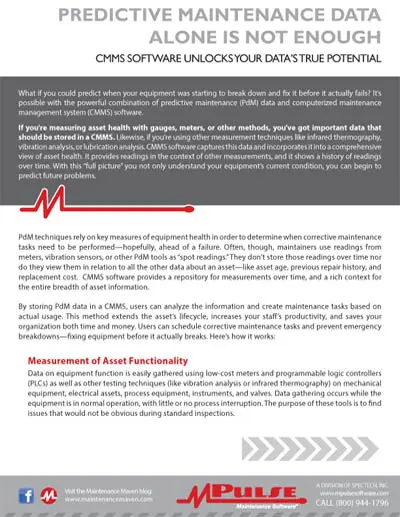
What if you could predict when your equipment was starting to break down and fix it before it actually fails?
It’s possible with the powerful combination of predictive maintenance (PdM) data and computerized maintenance management system (CMMS) software.
While PdM tools provide powerful data, that information’s value is limited without the context provided by CMMS software.
The combination of PdM data and a CMMS solution provides the most comprehensive view of your equipment.
Learn 5 important questions CMMS can help you answer to boost the effectiveness of your PM program.
MPulse System Requirements Datasheet
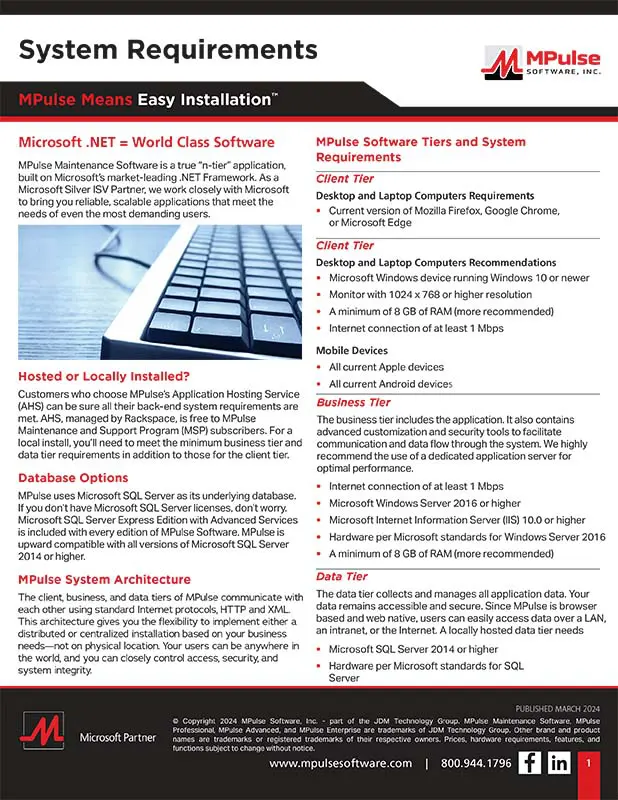
MPulse Maintenance Software is a true “n-tier” application, built on Microsoft’s market-leading .NET Framework.
As a Microsoft Silver ISV Partner, we work closely with Microsoft to bring you reliable, scalable applications that meet the needs of even the most demanding users.
The client, business, and data tiers of MPulse communicate with each other using standard Internet protocols, HTTP and XML.
This architecture gives you the flexibility to implement either a distributed or centralized installation based on your business needs—not on physical location.
Your users can be anywhere in the world, and you can closely control access, security, and system integrity.
MPulse Mobile
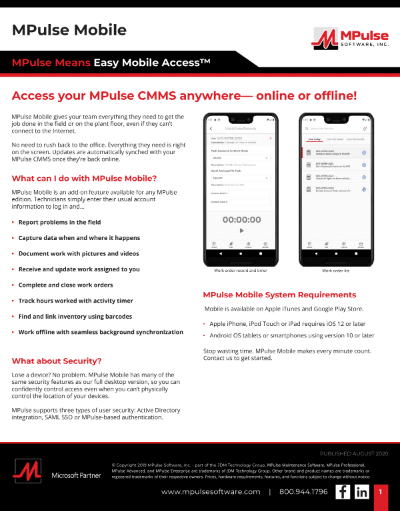
MPulse Means Easy Mobile Access Access your MPulse CMMS anywhere — online or offline! MPulse Mobile gives your team everything they need to get the
A Maintenance Manager’s Guide to the Industrial Internet of Things (IIoT)
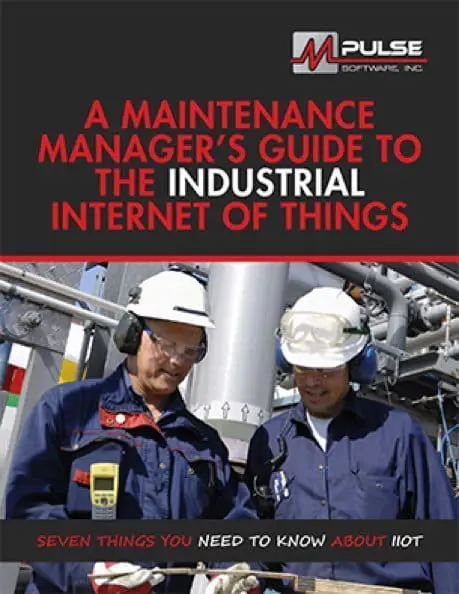
You’ve heard a lot about the IIoT for maintenance, but what does it mean for you? The IIoT is coming, and it will change how