10 Steps to a Successful CMMS Implementation
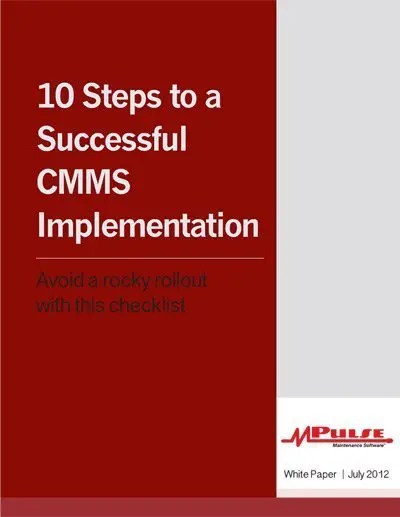
Avoid a rocky CMMS rollout with this CMMS implementation checklist.
CMMS (Computerized Maintenance Management System) technology has proven its ability to enhance business performance time and time again.
However, the path to effective CMMS implementation is not always easy—complexities often arise as a result of trying to align an entire company behind the concept..
You can find the success that comes from leveraging maintenance and asset data to the fullest measure by following these 10 steps to a successful CMMS implementation…
Manufacturing: Siemens Building Technologies Bolsters Plant Communications
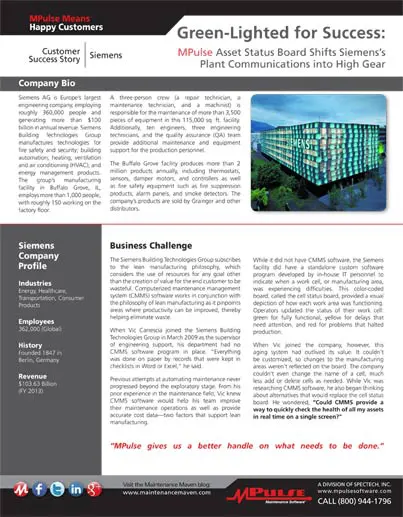
Find out how this $100-billion per year, 362,000-employee global behemoth uses MPulse to monitor its manufacturing assets in real time using MPulse Asset Status Board.
In the three years since the company implemented MPulse CMMS software, the Siemens Building Technologies Group has acheived:
- Work Order Completion Rate of 85-90% per month
- Preventative Maintenance Completion Rate of 100% per month
Siemens attributes much of the success to the strong relationship between the companies, which is built on collaboration.
Top 3 Signs You Need Life-Cycle Analysis
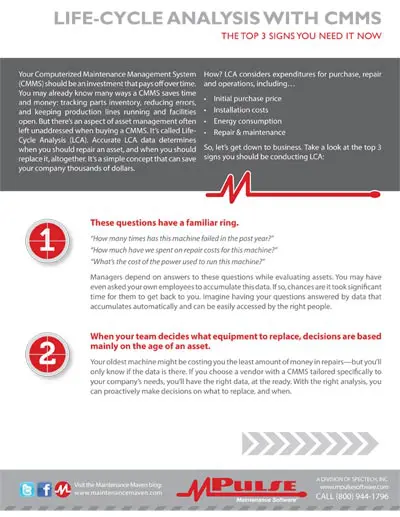
Your CMMS should be an investment that pays off over time.
You may already know many ways a CMMS saves time and money: tracking parts inventory, reducing errors, and keeping production lines running and facilities open.
But there’s an aspect of asset management often left unaddressed when buying a CMMS. It’s called LifeCycle Analysis (LCA).
Accurate LCA data determines when you should repair an asset, and when you should replace it, altogether.
It’s a simple concept that can save your company thousands of dollars. How?
Avoid a CMMS Implementation Fail
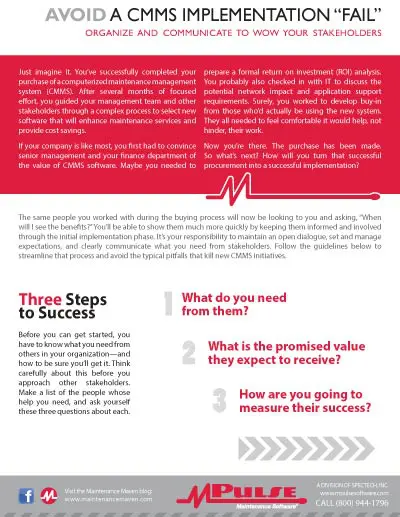
Do you know what steps to take to avoid an implementation disaster? Learn how to be hero instead of a zero with your new system.
Organize and Communicate to Wow Your Stakeholders
You’ve successfully completed your purchase of a computerized maintenance management system (CMMS).
If your company is like most, you first had to convince senior management and your finance department of the value of CMMS software.
Now you’re there. The purchase has been made.
So what’s next? How will you turn that successful procurement into a successful implementation?
Five Ways CMMS Can Save You Money
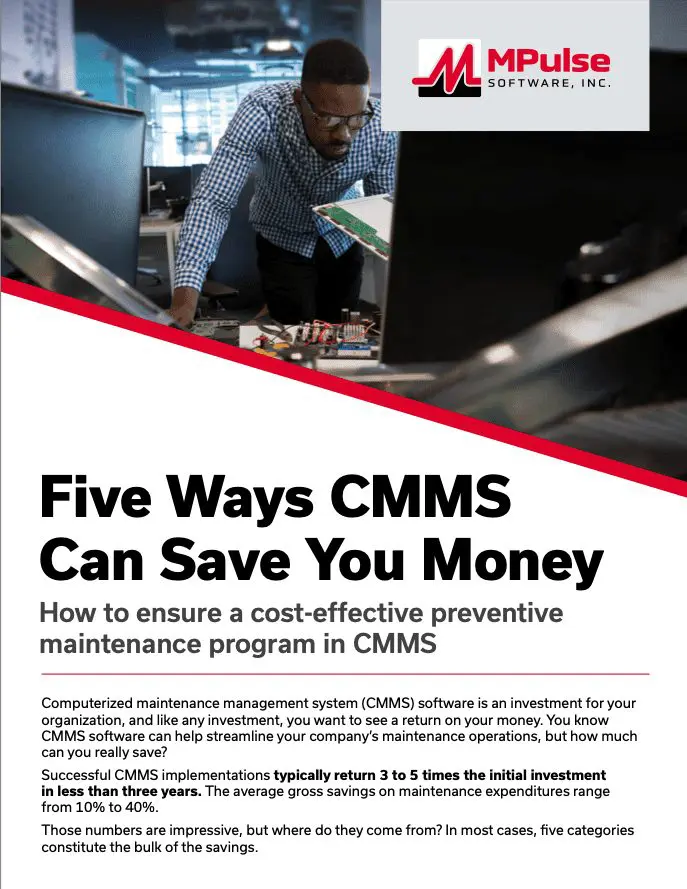
Show me the money!
Computerized maintenance management software (CMMS) is an investment for your organization, and like any investment, you want to see a return on your money.
You know computerized maintenance management software can help streamline your company’s maintenance operations, but how much can you really save?
Successful CMMS implementations typically return 3 to 5 times the initial investment in less than three years. The average gross savings on maintenance expenditures range from 10% to 40%.
Those numbers are impressive, but where do they come from? In most cases, five categories constitute the bulk of the savings.
Use Your CMMS Power Wisely
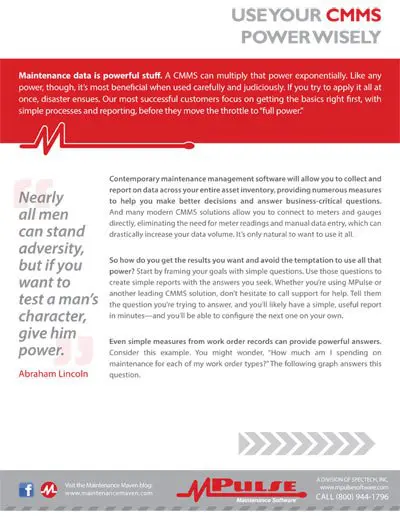
Maintenance data is powerful stuff. A CMMS can multiply that power exponentially.
Like any power, though, it’s most beneficial when used carefully and judiciously. If you try to apply it all at once, disaster ensues.
So how can you keep your reporting simple and focused on the questions that matter most to you?
Our most successful customers focus on getting the basics right first, with simple processes and reporting, before they move the throttle to “full power.”
Learn how.
CMMS By The Numbers
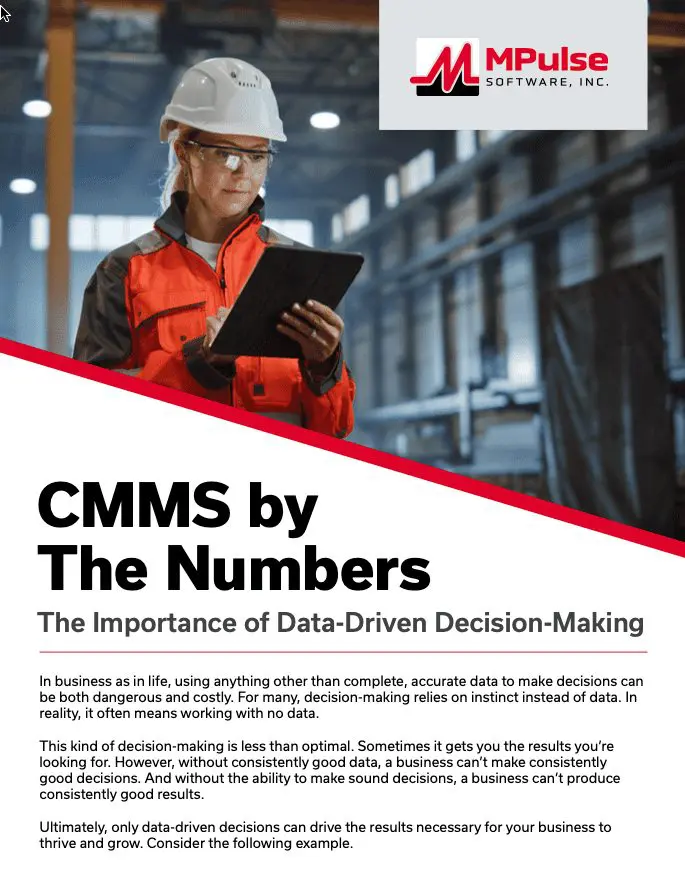
Don’t rely on intuiting the right answers for your critical business decisions. Your CMMS is a treasure trove of valuable information.
Without consistently good data, a business can’t make consistently good decisions. And without the ability to make sound decisions, a business can’t produce consistently good results.
Ultimately, only data-driven decisions can drive the results necessary for your business to thrive and grow.
Ask yourself whether it’s possible to support your decisions with numbers. You’ll quickly see the results in the most important place of all—your bottom line.
Simple Preventive Maintenance Can Boost PM Effectiveness
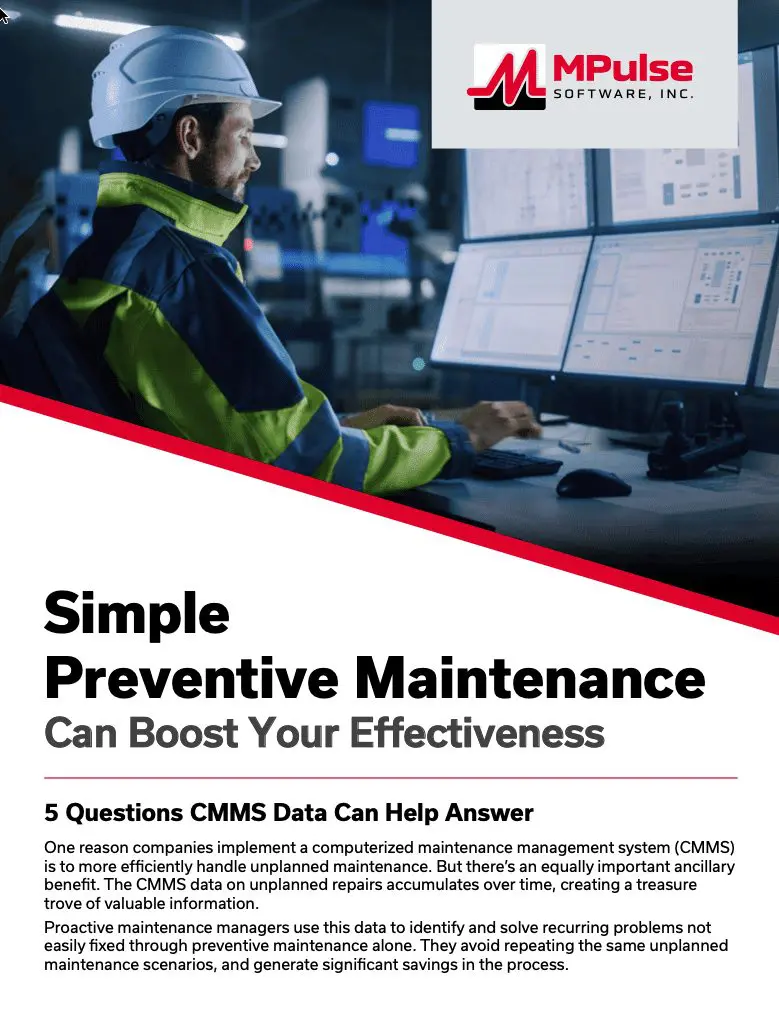
One reason companies implement a CMMS is to more efficiently handle unplanned maintenance.
But there’s an equally important benefit. The CMMS data on unplanned repairs accumulates over time, creating a treasure trove of valuable information.
Proactive maintenance managers use this data to identify and solve recurring problems not easily fixed through preventive maintenance alone.
They avoid repeating the same unplanned maintenance scenarios, and generate significant savings in the process.
Learn how to identify these “invisible”problems—and to make the repairs needed before they result in more expensive unplanned repairs and production downtime.
Manufacturing: Turn-Key Data Integration that “Just Works” for Saint-Gobain’s Ceramics
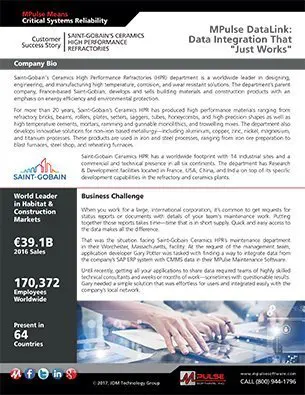
When you work for a large, international corporation, it’s common to get requests for status reports or documents with details of your team’s maintenance work.
Putting together those reports takes time—time that is in short supply. Quick and easy access to the data makes all the difference.
That was the situation facing Saint-Gobain Ceramics HPR’s maintenance department in their Worchester, Massachusetts, facility. At the request of the management team, application developer Gary Potter was tasked with finding a way to integrate data from the company’s SAP ERP system with CMMS data in their MPulse Maintenance Software.
Until recently, getting all your applications to share data required teams of highly skilled technical consultants and weeks or months of work—sometimes with questionable results.
Gary needed a simple solution that was effortless for users and integrated easily with the company’s local network.
Satellite Services: The Industrial Internet of Things (IIoT) Delivers a Competitive Edge
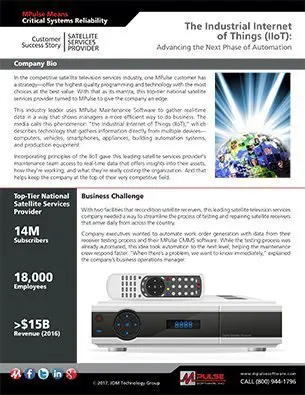
In the competitive satellite television services industry, one MPulse customer has a strategy—offer the highest quality programming and technology with the most choices at the best value.
With that as its mantra, this top-tier national satellite services provider turned to MPulse to give the company an edge.
This industry leader uses MPulse Maintenance Software to gather real-time data in a way that shows managers a more efficient way to do business. The media calls this phenomenon “the Industrial Internet of Things (IIoT),” which describes technology that gathers information directly from multiple devices— computers, vehicles, smartphones, appliances, building automation systems, and production equipment.
Incorporating principles of the IIoT gave this leading satellite services provider’s maintenance team access to real-time data that offers insights into their assets, how they’re working, and what they’re really costing the organization. And that helps keep the company at the top of their very competitive field.