Home > What is a Work Order?
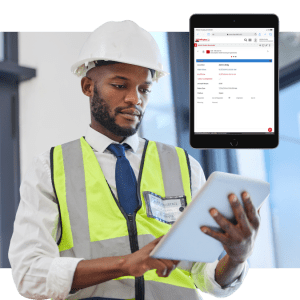
Understanding the Key to Efficient Maintenance Management
Whether you’re managing routine inspections or urgent repairs, MPulse Software makes the entire work order lifecycle simpler and more effective.
Table of Contents
What is a Work Order?
A work order is a document that outlines the details of maintenance tasks, guiding their execution. It’s a crucial tool in an organization’s maintenance strategy, ensuring tasks are completed efficiently and effectively.
When a maintenance request is made, a work order is created, containing key information like:
The company handling the task
The location of the work
Required skills, tools, and materials
The authorizing party
The technician or service provider assigned
Estimated and actual completion dates
Priority level and cost estimates
The main purpose of a work order is to streamline communication and ensure the smooth execution of tasks. When used effectively, it helps improve organization, track progress, and enhance team communication.
Types of Work Orders
Different types of work orders are used depending on the size and industry of the organization. Here are eight common types:
- Corrective Maintenance: Addresses issues found during inspections or operations, involving repairs or replacements.
- Electrical: Used for electrical system repairs or installations, such as wiring or lighting.
- Emergency: Issued when critical equipment fails and disrupts production or creates safety hazards.
- General: For routine, non-urgent tasks like pest control or painting.
- Inspection: Issued for routine equipment inspections to prevent issues before they occur.
- Preventive Maintenance: Schedules regular maintenance to keep equipment in optimal condition and prevent costly repairs.
- Safety: Focuses on preventing hazards and ensuring worker safety.
- Special Project: Used for upgrades or improvements, modernizing equipment or processes.
The Work Order Lifecycle
Every work order goes through a lifecycle, which consists of three main phases: creation, completion, and recording. These phases break down into six steps:
Task Identification
Identify the need for maintenance, either planned or unplanned.
Work Request
Create and submit a formal work request. The work request may be digital or written.
Prioritization and Scheduling
Assign priorities and set deadlines based on urgency and resources.
Assignment and Completion
Assign the task to a technician and complete the work.
Documentation and Closure
Once completed, close the work request and document the details for future reference.
Analysis and Review
Analyze and identify improvements for future tasks and prevent recurring issues.
Key Components
A well-written work order contains 16 key components, ensuring that the task is completed effectively and efficiently:
- Asset: The equipment needing attention
- Description of Issue: Detailed issue explanation
- Scope of Work: Task details
- Parts and Tools Required: Necessary materials
- Health and Safety Notes: Safety procedures
- Date Requested: Work request creation date
- Requester Information: Requestor’s details
- Expected Completion Date: Task deadline
- Actual Completion Date: Actual completion time
- Hours of Work: Estimated vs. actual time taken
- Task Checklist: Step-by-step guide
- Priority: Urgency of the task
- Assigned to: Technician or team
- Associated Documents: Manuals, diagrams, etc.
- Notes: Additional observations
Paper vs. Digital
While traditional paper work orders are still used in some organizations, digital work orders provide many advantages. Switching from paper to digital offers numerous benefits, such as:
- Efficient Completion: Digital work orders streamline the process by providing instant access to documents and resources, reducing travel time and improving technician efficiency.
- Reduced Storage Costs: No need for physical space to store documents.
- Improved Accessibility: Easily accessed via a mobile device, enabling technicians to find the information they need quickly and without hassle.
- More Visible Data: Real-time tracking and better visibility of maintenance data, which can be automatically pulled into dashboards for reporting.
- Lower Labor and Planning Costs: Digital systems make management easier, saving time in data entry, scheduling, and resource allocation.
What is Work Order Management Software?
Work order management software helps organizations create, track, and schedule maintenance tasks more effectively. It simplifies the lifecycle, reducing manual paperwork and ensuring smoother operations. This software is especially useful in industries with high volumes of work orders, allowing teams to track and manage requests with ease.
How Different Industries Use Work Order Management Software
Manufacturing: Tracks and schedules maintenance tasks, including repairs and preventive maintenance.
Housing: Manages tenant or staff maintenance requests, scheduling work for service providers.
Contractors: Logs customer requests, tracks materials, and manages labor costs.
In summary, using work orders—whether manually or with management software—ensures maintenance tasks are completed efficiently and in a timely manner, improving overall operational success.
MPulse Means Happy Customers
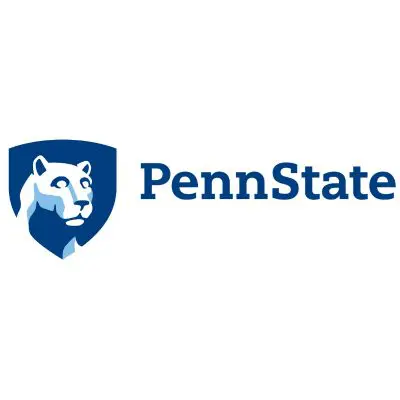
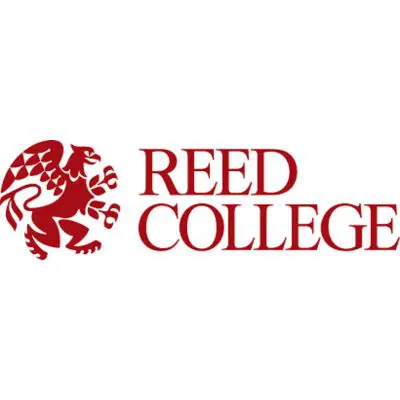
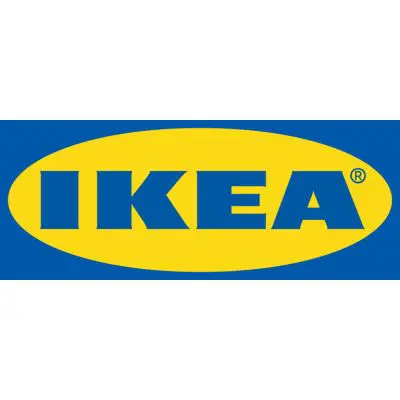
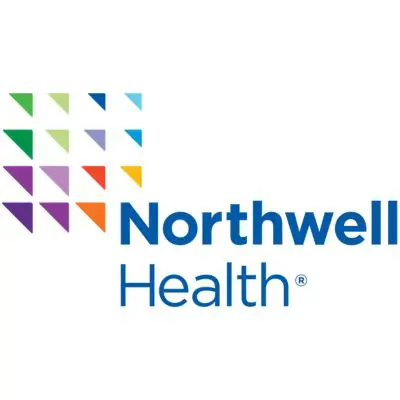
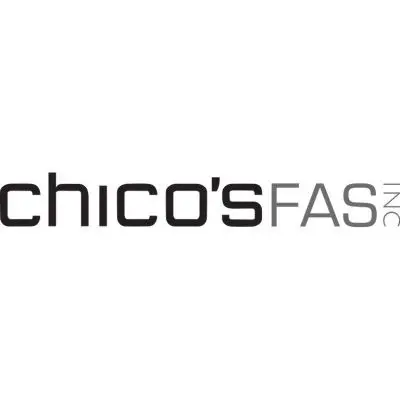
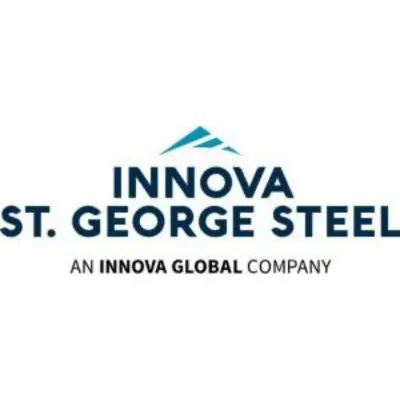