Home > Resources > Learning Center > What is Planned Maintenance?
What is Planned Maintenance?
Planned Maintenance, or Preventive Maintenance, empowers teams to keep assets running smoothly by addressing issues before they happen. With real-time planning and automation, MPulse Software helps you create a planned maintenance program by organizing tasks, tracking progress, and reducing risks to your operations. Start optimizing reliability today with a smarter maintenance strategy.
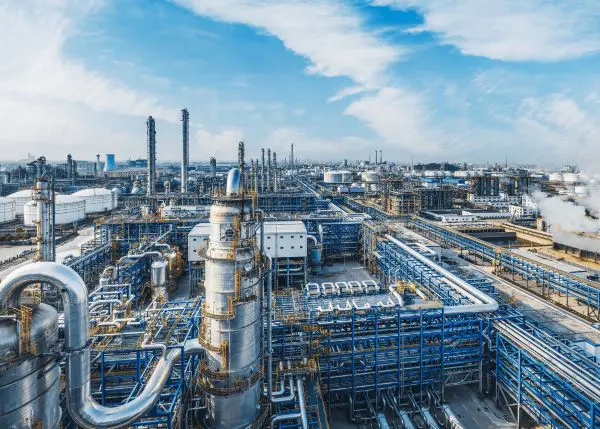
Planned Maintenance increases efficiency and reduces risks
Planned Maintenance (also known as Preventive Maintenance) helps maintenance technicians avoid failures by fixing equipment before it breaks. Use data to plan your preventative maintenance. This ensures increased efficiency and reduces risks.
Planned maintenance minimizes downtime and boosts operational efficiency for long-term success. Every piece of equipment, like HVAC systems or facility tools, needs routine care. Maintenance requires attention to every asset type
A CMMS helps manage planned maintenance schedules and improves workflow. CMMS tools help manage work orders, track preventive maintenance tasks, and support asset facilities management. Use CMMS to boost asset performance and drive cost savings through performance maintenance.
Preventive maintenance tasks begin with PMs. These are also called planned work orders. Manage planned work orders easily with CMMS software. Once your maintenance crew selects CMMS Software, you can decide whether your planned schedule will be usage-based or time frame-based. What is planned maintenance? It’s like a health check for machines and teams—done regularly to avoid breakdowns.
Some issues are use-based (hours, cycles, mileage, etc..), others need time-based maintenance (weekly, monthly, annually, etc..). Identify patterns to create better maintenance strategies.
Whether you use timed or metered based schedules, good planned maintenance reduces emergency repairs. MPulse helps ensure equipment stays reliable with less downtime.
Table of Contents
Planned Maintenance Categories
Time-Based Maintenance
Implementing a planned maintenance program helps minimize downtime and ensures equipment reliability, making it a top maintenance schedule example across industries.
One of the simplest planned maintenance examples is time-based maintenance, also known as calendar-based maintenance. This method involves scheduling tasks like inspections, lubrication, or cleaning at regular intervals, based on a predefined maintenance schedule. It’s a classic example that answers the question, what is planned maintenance in its most traditional form. By adhering to this schedule, organizations can proactively address potential issues before they lead to costly breakdowns.
Usage-Based Maintenance
This approach emphasizes asset usage rather than adhering to a fixed schedule, making it a valuable component of a planned maintenance strategy. Understanding your processing time is key to optimizing your maintenance schedule and achieving greater uptime through smarter maintenance scheduling. Still unsure what planned maintenance method aligns with evolving workloads? This strategy covers all bases.
This approach aligns more closely with the actual condition of the equipment, making it an integral part of a robust planned maintenance program. It’s ideal for identifying potential problems early and tackling them proactively through routine maintenance scheduling to avoid costly downtime. Are your physical assets showing signs of needed repairs, such as increased noise levels or longer startup times? A planned maintenance strategy can help you catch these issues before they become major disruptions. CBM is a critical part of a maintenance schedule—by allowing you to act when it truly matters. It minimizes guesswork and ensures that physical assets don’t fall apart unexpectedly. Condition Based Maintenance helps you avoid reactive repairs and optimize performance without wasting resources.
Predictive Maintenance
Here’s where technology truly shines. As a top-tier planned maintenance example, predictive maintenance uses smart tools to monitor equipment and execute maintenance scheduling only when needed. This approach saves time, minimizes downtime, and enhances operational efficiency—a win-win! Predictive maintenance factors in lead time, processing time, latency, and performance testing, utilizing cutting-edge technology integrated with compatible CMMS software. To maximize its benefits, ensure your CMMS software is fully compatible with the predictive maintenance tools you’re using. Combine PdM with real-time insights and you’ve got a power-packed strategy.
Risk-Focused Maintenance
This approach combines elements of condition-based and predictive maintenance, making it a vital component of a comprehensive planned maintenance program. It helps redefine what is routine maintenance by shifting the focus from fixed intervals to strategic prioritization. By focusing on the criticality of assets, it ensures that high-risk equipment receives the extra attention it needs to minimize the likelihood of major failures. This planned maintenance strategy prioritizes resources, helping reduce risk and offering one of the best planned maintenance examples in asset care. It is a top-tier strategy with real risk-reduction benefits. With a planned maintenance program tailored to emphasize critical assets, organizations can enhance reliability, extend equipment lifespan, and reduce unplanned downtime.
RxM Powered by AI
Think of this as maintenance with a crystal ball. By incorporating AI, machine learning, and advanced analytics, this approach enhances your planned maintenance program and addresses key concerns related to a maintenance schedule. You might initially think, ‘That sounds expensive,’ but while costs can vary, this method often leads to significant savings by reducing downtime and preventing costly breakdowns—especially if it aligns well with your maintenance strategy.
Learn about CMMS Software that can lower costs for manufacturers.
Benefits of Implementing a Planned Maintenance Program
Now that the question “What is Planned Maintenance?” has been answered, explore how implementing a planned maintenance program supported by MPulse CMMS can help you:
Simplify Maintenance
MPulse Software streamlines maintenance operations by automating reminders, generating schedules, and providing a centralized platform for tracking and managing planned maintenance tasks.
Proactive Approach
Shift from reactive to planned maintenance, allowing you to address issues before they become critical and impact your operations.
Increase Efficiency
By reducing unplanned downtime and optimizing asset performance, you can increase productivity and operational efficiency.
Data-Driven Decisions
Gain insights into asset performance, maintenance history, and trends through comprehensive reporting and analytics. Make informed decisions to improve maintenance strategies and resource allocation.
Scalable Solution
MPulse Software is scalable and adaptable, whether you have a small maintenance team or a large enterprise. You can customize the software to fit your unique requirements and grow with your business.
Creating a Planned Maintenance Schedule
Implementing planned measures begin by establishing a maintenance schedule. Managing tasks, schedules, and processes can feel overwhelming, but the right CMMS software can make a significant difference. Choose software that offers powerful planning options to automate and enforce your planned maintenance
Frequently Asked Questions About MPulse Software for Planned Maintenance
Why Do I Need Planned Maintenance?
The MPulse CMMS planned maintenance program allows you to automate and enforce your planned maintenance, simplifying adherence to manufacturer and compliance guidelines. These schedules and inspections help spot issues before they occur, minimizing costly disruptions. Maintenance intervals can be set based on time, operating hours, or part condition—triggering work orders just before inefficiencies or failures arise.
The program also ensures equipment is properly calibrated, lubricated, and maintained at the right time. Properly cared-for assets perform more efficiently, consume less energy, and fail less often—significantly extending their usable life. By establishing and consistently performing planned maintenance procedures, organizations can avoid serious problems caused by neglect and delay the need for costly repairs or replacements.
Learn how you can ensure your success with planned maintenance software.
What’s the difference between Planned Maintenance and Predictive Maintenance?
Planned maintenance is triggered by time, meter, or event. This type of maintenance is based on average or expected life statistics (usually determined by the equipment manufacturer or vendor). The most common example is changing the oil in a car every 5,000 miles or every 6 months.
Planned maintenance is one of the first steps to reduce run-to-failure maintenance in favor of a more proactive maintenance program. Additionally, CMMS programs excel at helping maintenance shops schedule preventive maintenance tasks, preventing failure and prolonging asset life cycles.
Predictive maintenance means different things to different people. Usually, maintenance professionals define it as gathering data on the actual condition of equipment to determine when maintenance is needed, sometimes called condition-based maintenance (CBM). CBM allows you to track meters and gauges on assets and to trigger work orders at specific points. You can gather the data manually or automatically, and your CMMS software stores the data and alerts maintenance staff to take action.
For example, condition-monitoring tools and CMMS software can analyze how the asset is working—maybe by measuring operating temperatures, vibration frequencies, or miscleaneous pressures, etc. This data helps spot signs of potential problems. Then CMMS software sends alerts before breakdowns occur.
Discover how simple predictive maintenance can boost PM effectiveness.
What Planned Maintenance features are available in MPulse CMMS?
These eight features should be available in Planned maintenance software…
- Asset Records store details about equipment, buildings, vehicles, rooms, and grounds—asset name, purchase date, purchase price, serial number, location, and other important details.
- Employee Records store information about your employees—names, contact information, certifications, etc.
- Inventory Records record details about spare parts and consumables you have on hand—type, model, serial number, manufacturer, supplier name, location name, item number, item state, unit of measure, OH quantity etc.
- Work Orders link all the elements of repair and maintenance work in one place.
- Inventory Management helps you keep up with the spare parts and consumables you have on hand.
- Reporting tools help you create meaningful information from the data recorded for assets, employees, inventory, schedules, and work orders.
- Scheduling enables you to establish, monitor, and execute planned maintenance tasks (both time- and meter-based).
- Service Requesting is essential when you get repair requests from either internal departments or outside customers—allowing users to enter and initiate service requests, and then monitor the progress of the requests as your team completes repairs.
How much does Planned Maintenance and Tracking software cost?
Software prices vary significantly depending on your needs and the size of your operations. Typically, you’ll pay for the base software and then the number of licenses you need. Advanced features also will add to the cost.
The software cost is more than just the price of the software itself. When you ask for a software quote, plan to include…
- Startup training
- Integration services
- Data migration from legacy systems
- Hosting
- Maintenance/support agreements
The best way yo compare CMMS cost is to calculate and compare the total five-year total cost of ownership of all these things to get an accurate comparison.
What’s the difference between Timed vs. Metered Planned Maintenance with CMMS Software?
Timed planned maintenance is simply based on the time between PM tasks—such as days, weeks, months, etc. A good example is inspections, which need to be performed at specific time intervals to help maintenance teams spot issues before they occur.
Metered PM scheduling measures usage using a specific meter, which triggers a PM task at the appropriate time. Meter readings track and measure the cumulative values of equipment, machinery, vehicles, and other assets—such as mileage, hours, cycles, injection counts, etc.
Over time these meter readings create historical data for the asset, which maintenance managers can use to determine if repairs were successful or if they should adjust the PM schedule based on performance.
Learn how to automate meter readings with MPulse DataLink.
Preventive maintenance involves regular, scheduled upkeep to prevent equipment failures before they occur. It reduces unexpected breakdowns, extends the lifespan of assets, and lowers overall maintenance costs. A CMMS makes implementing preventive maintenance easier by automating schedules and tracking work history.
Learn how you can ensure your success with preventive maintenance software.