MPulse CMMS
Preventive Maintenance Software for Efficient and Cost Effective Operations
Maximize asset lifespan, reduce downtime, and streamline maintenance processes with MPulse Preventive Maintenance Software. Proactively address potential issues, ensure equipment reliability, and keep your operations running smoothly with ease and efficiency.
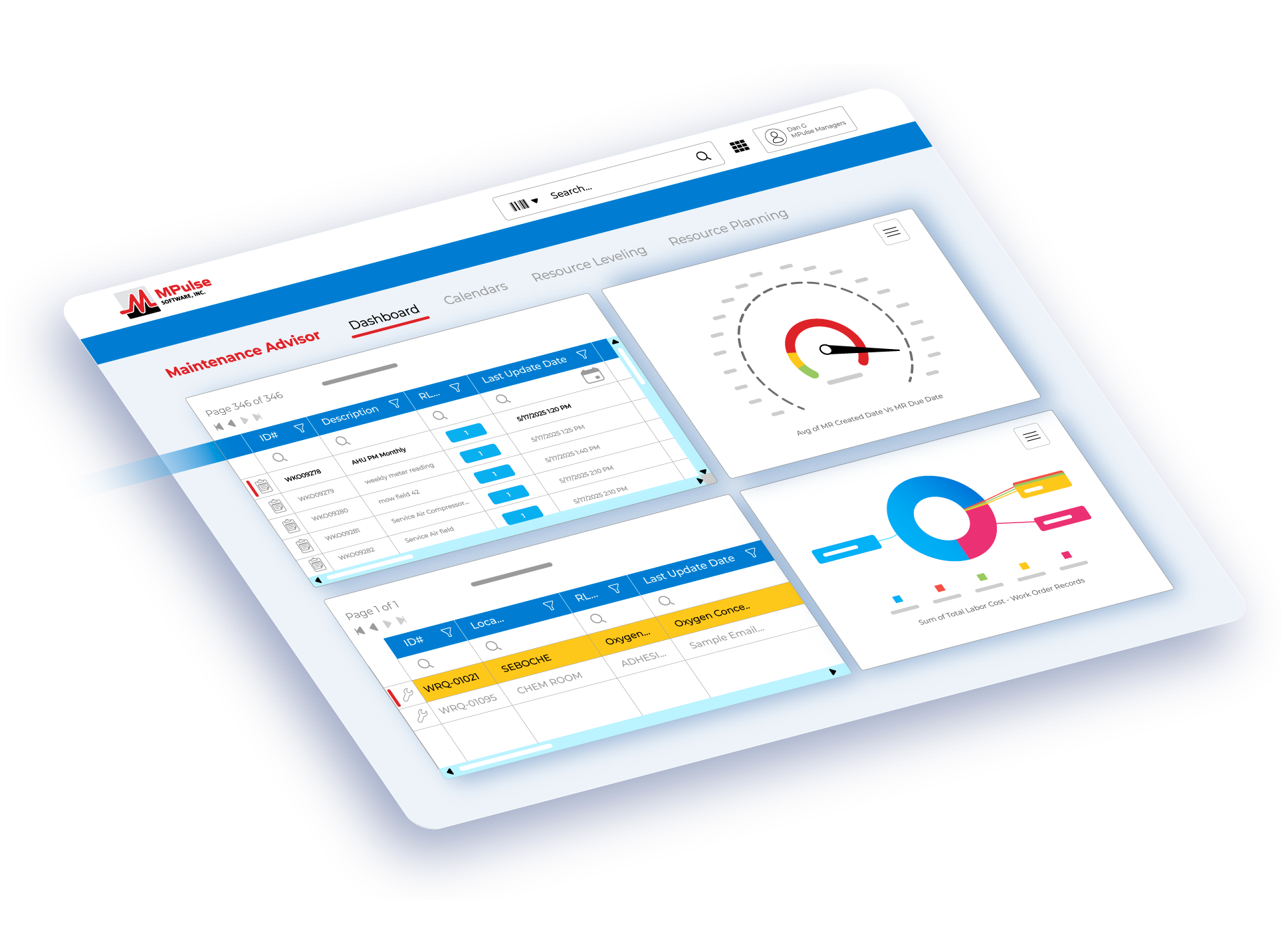
The Power of Preventive Maintenance and MPulse Software
Maintaining your assets is essential for maximizing their lifespan and minimizing unexpected breakdowns. Traditional reactive maintenance approaches can result in costly repairs, increased downtime, and decreased productivity. It’s time to shift to a proactive and preventive maintenance strategy that empowers you to stay ahead of issues and optimize your operations.
With automated maintenance reminders, preventive maintenance scheduling capabilities, and comprehensive tracking features, you can take control of your assets’ health and reduce downtime with MPulse Software.
Why Choose MPulse Software for Preventive Maintenance
Preventive Maintenance for Extend Asset Lifespan and Reduce Downtime
MPulse preventive maintenance software enables you to extend the lifespan of your assets by implementing regular maintenance routines. By proactively addressing potential issues, you can prevent costly breakdowns and ensure optimal performance, resulting in reduced downtime and increased productivity.
Automated Maintenance Reminders and Scheduling
MPulse Software automates preventive maintenance reminders based on predefined schedules, equipment usage, or other factors. With our comprehensive preventive maintenance program, you can effortlessly generate and manage maintenance schedules, ensuring timely execution of tasks to keep your assets in peak condition. Proactively address potential issues, extend asset lifespan, and minimize downtime with ease.
Benefits of Implementing CMMS Software for Preventive Maintenance
Simplify Maintenance
MPulse Software streamlines maintenance operations by automating preventive maintenance reminders, generating schedules, and providing a centralized platform for tracking and managing preventive maintenance tasks.
Proactive Approach
Shift from reactive to preventive maintenance, allowing you to address issues before they become critical and impact your operations.
Increase Efficiency
Preventive maintenance reduces unplanned downtime and optimizes asset performance, resulting in increased productivity and operational efficiency.
Data-Driven Decisions
Gain insights into asset performance, maintenance history, and trends through comprehensive reporting and analytics. Make informed decisions to improve preventive maintenance strategies and resource allocation.
Scalable Solution
MPulse CMMS is scalable and adaptable, whether you have a small maintenance team or a large enterprise. Customize the software to fit your unique requirements and grow with your business.
Who Uses MPulse Software for Preventive Maintenance?
MPulse helps our customers keep facilities operating at peak efficiency and manufacturing assets working at maximum productivity. MPulse is designed to grow with any size business, from small organizations with one or two maintenance technicians to global enterprises with locations around the world.
We have served more than 2,700 customers since 1995. MPulse customers include a long list of household names like Verizon, Rolex, General Dynamics, Fender Guitars, Toyota, and Siemens. Our customers are located across all 50 U.S. states and in 22 additional countries around the world … including a research station in Antarctica!
We like to say, with a wink, “We only serve companies who work in buildings or make something.” Our customers work in a wide range of industries, such as manufacturing, facility management, healthcare, transportation, government, energy, education, recreation, mining and fabrication.
Frequently Asked Questions About Preventive Maintenance Software
Why Do I Need Preventative Maintenance Software?
Our preventive maintenance program ensures an automatic schedule of PM tasks, simplifying adherence to manufacturer guidelines. These schedules and inspections help spot issues before they occur, minimizing costly disruptions. Maintenance intervals can be set based on time, operating hours, or part condition—triggering work orders just before inefficiencies or failures arise.
The program also ensures equipment is properly calibrated, lubricated, and maintained at the right time. Properly cared-for assets perform more efficiently, consume less energy, and fail less often—significantly extending their usable life. By establishing and consistently performing preventive maintenance procedures, organizations can avoid serious problems caused by neglect and delay the need for costly repairs or replacements.
Learn how you can ensure your success with preventive maintenance software.
What Are the Features I'll Need for Preventative Maintenance Software?
These eight features should be available in preventive maintenance software…
- Asset Records store details about equipment, buildings, vehicles, or other assets—asset name, purchase date, purchase price, serial number, location, and other important details.
- Employee Records store information about your employees—names, contact information, certifications, etc.
- Inventory Records record details about spare parts and consumables you have on hand—type, model, serial number, manufacturer, supplier name, location name, item number, item state, unit of measure, etc.
- Work Orders link all the elements of repair and maintenance work in one place.
- Basic Inventory Management helps you keep up with the spare parts and consumables you have on hand.
- Basic Reporting tools help you create meaningful information from the data recorded for assets, employees, inventory, schedules, and work orders.
- Scheduling enables you to establish, monitor, and execute PM tasks (both time- and meter-based).
- Service Requesting is essential when you get repair requests from either internal departments or outside customers—allowing users to enter and initiate service requests, and then monitor the progress of the requests as your team completes repairs.
How much does PM Scheduling and Tracking software cost?
Software prices vary significantly depending on your needs and the size of your operations. Typically, you’ll pay for the base software and then the number of licenses you need. Advanced features also will add to the cost.
The software cost is more than just the price of the software itself. When you ask for a software quote, plan to include…
- Startup training
- Integration services
- Data migration from legacy systems
- Hosting
- Maintenance/support agreements
Calculate the five-year total cost of ownership of all these things to get an accurate comparison.
These price range estimates will tell you if their product is a good fit.
What’s the difference between Preventive Maintenance vs. Predictive Maintenance?
Preventive maintenance is triggered by time, meter, or event. This type of maintenance is based on average or expected life statistics (usually determined by the equipment manufacturer or vendor). The most common example is changing the oil in a car every X,000 miles or every X months.
Preventive maintenance is one of the first steps to reduce run-to-failure maintenance in favor of a more proactive maintenance program. Additionally, CMMS excels at helping maintenance shops schedule preventive maintenance tasks, preventing failure and prolonging asset life cycles.
Predictive maintenance means different things to different people. Usually, maintenance professionals define it as gathering data on the actual condition of equipment to determine when maintenance is needed—sometimes called condition-based maintenance (CBM). CBM allows you to track meters and gauges on assets, and to trigger work orders at specific points. You can gather the data manually or automatically, and your CMMS software stores the data and alerts maintenance staff to take action.
For example, condition-monitoring tools and CMMS software can analyze how the asset is working—maybe by measuring operating temperature or oil viscosity, etc. This data helps spot signs of potential problems. Then CMMS software sends alerts before breakdowns occur.
Discover how simple predictive maintenance can boost PM effectiveness.
What’s the difference between Timed vs. Metered Preventive Maintenance with CMMS Software?
Timed preventive maintenance is simply based on the time between PM tasks—such as days, weeks, months, etc. A good example is inspections, which need to be performed at specific time intervals to help maintenance teams spot issues before they occur.
Metered PM scheduling measures usage using a specific meter, which triggers a PM task at the appropriate time. Meter readings track and measure the condition of equipment, machinery, vehicles, and other assets—such as mileage, usage time, production volume, pressure, flow rate, etc.
Over time these meter readings create historical data for the asset, which maintenance managers can use to determine if repairs were successful or if they should adjust the PM schedule based on performance.
Learn how to automate meter readings with MPulse DataLink.
MPulse Software Blog
MPulse Means Happy Customers
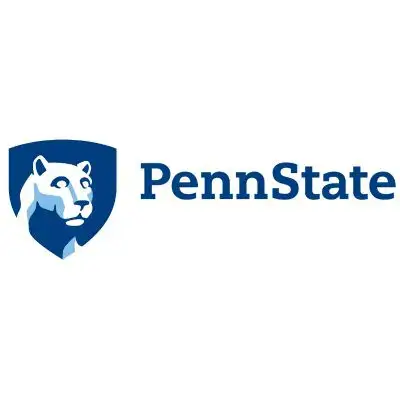
“The features and price made MPulse the right choice and the service has been excellent.”
John Smith
Maintenance Supervisor, Penn State University
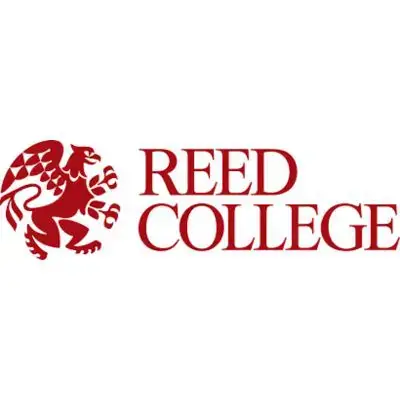
“You can tailor the program to fit the needs of your particular facility. The performance of the software is overall very good.”
Maintenance Manager
Reed College
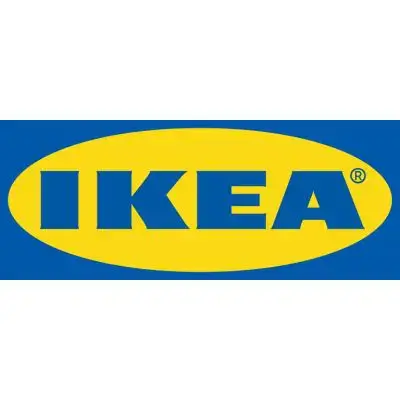
“I started using MPulse in March of 2006 using v6. The upgrade to v7 has been a smooth and easy transition offering more of the features that are needed by my sites.”
Facilities Manager
IKEA US West Inc.
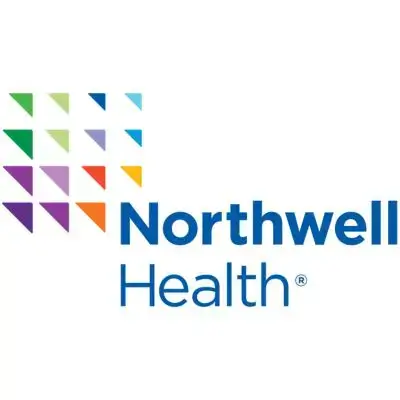
“It certainly has simplified keeping track of what we do and how we do it.”
Director of Engineering
Real Estate Services, Northwell Health
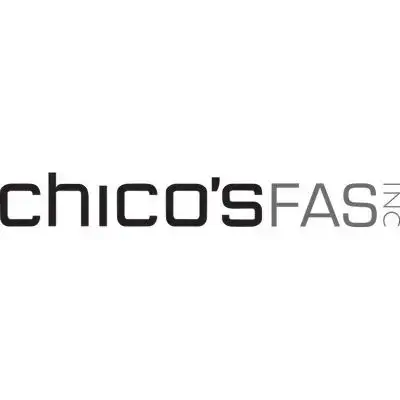
“MPulse has been with us every step of the way as our business expanded. Consistently outstanding service.”
Facilities Coordinator
Distribution Center, Chicos FAS, Inc.
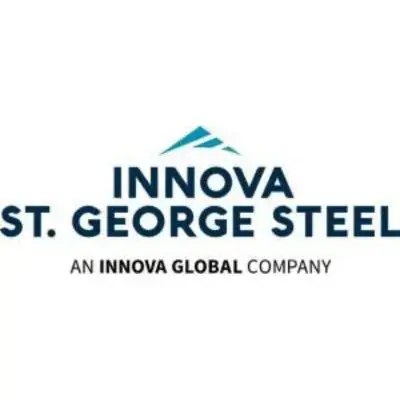
“When you use pencil and paper, it takes hours. It takes a lot of time to get a result, where it only takes minutes in software like MPulse.”
Executive Administrative Assistant
St. George Steel